CUSTOM SADDLE TREES
JR Wenger Custom Saddles is proud to announce that we make our own saddle trees. In 2015 after consistently being let down by other companies saddle trees, we decided it was time to make our own. By doing so, we have gained a competitive edge in the marketplace and also added to our business by selling directly to other manufacturers. Our saddle trees can provide custom total custom fits and are not limited by what we can purchase from other factories like most of our competitors. We have been promoting saddle fit since the day we started and we believe that in the pleasure horse industry it is just as important, if not more important than other disciplines. JR Wenger custom saddles is able to produce a limited number of trees for outside sales, based on our customers specific needs. If you are interested in purchasing our saddle trees please contact us directly.
Step one in our saddle tree process
PRODUCTION METHOD
We proudly make two styles, traditional rawhide covered and hand laid fiberglass covered. The saddle tree production process starts off by using Poplar wood and sawing tree parts on duplicator saws, creating a blocked out pattern. Then the parts are trimmed and sanded to the final measurements and are now ready for assembly. The parts are then placed in the jig which is set up to our customers specs. Finally, the parts are screwed together and the horn is applied, and it is ready for the covering.
Rawhide being applied to custom tree
RAWHIDE COVERED
From here we will cover the tree in either rawhide or fiberglass depending on our customers needs. If rawhide is what is needed, we will trim the rawhide then hand sew it to the tree. After the rawhide is dry we will nail in place, and cover with a lacquer finish.
Finished fiberglass tree ready to be used for a new saddle
FIBERGLASS FINSH
If fiberglass is what the customer is wanting we will hand lay the glass on the trees and a special resin is applied, giving it our trademark look of bright red. After they are dry we will sand them and build in the ground seat for added strength. Finally, we apply an extra couple coats of resin and they are ready to either be shipped to the customer, or head over to the saddle shop where they will turn into a custom saddle.
COMPLETE PROCESS
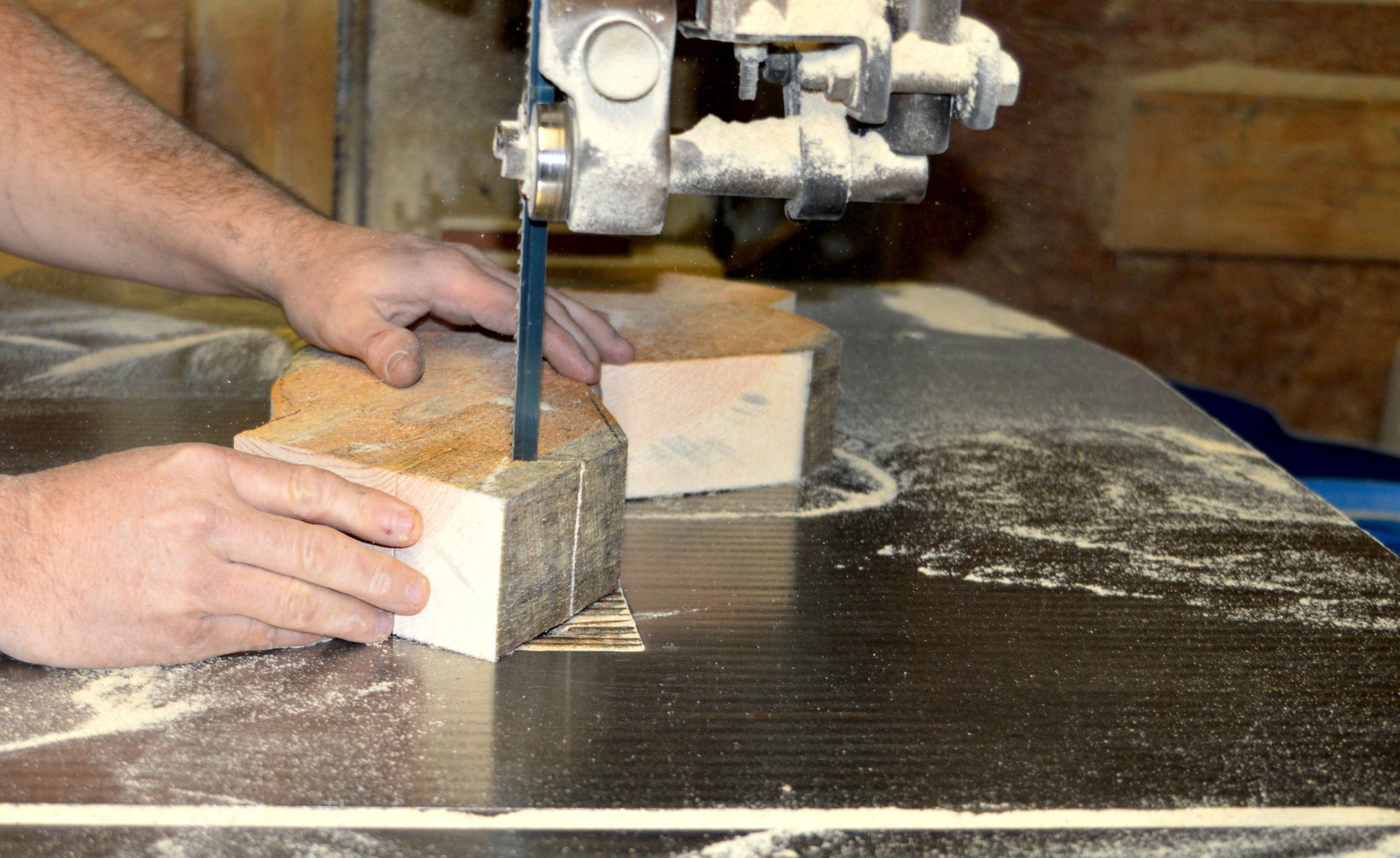
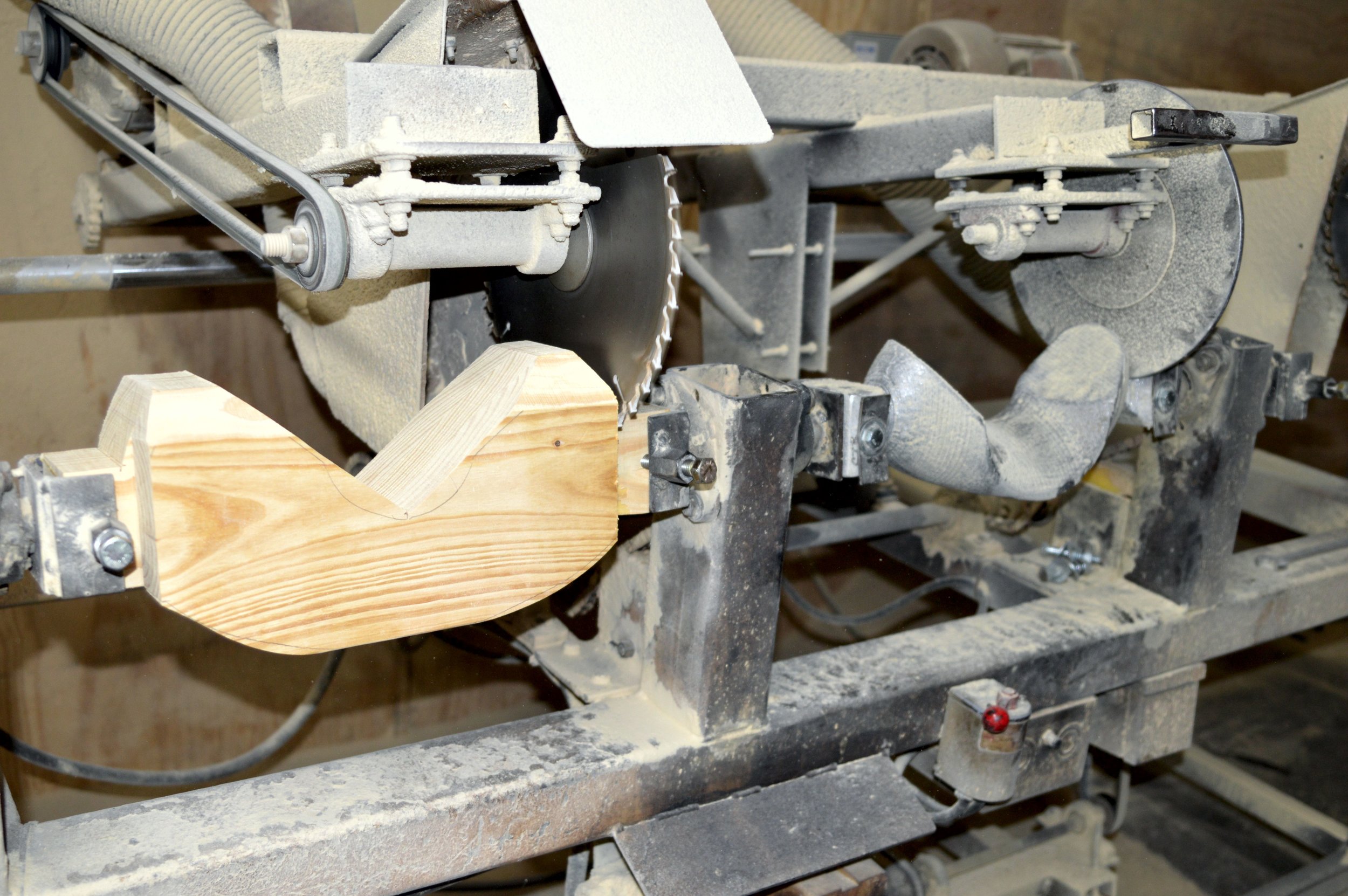
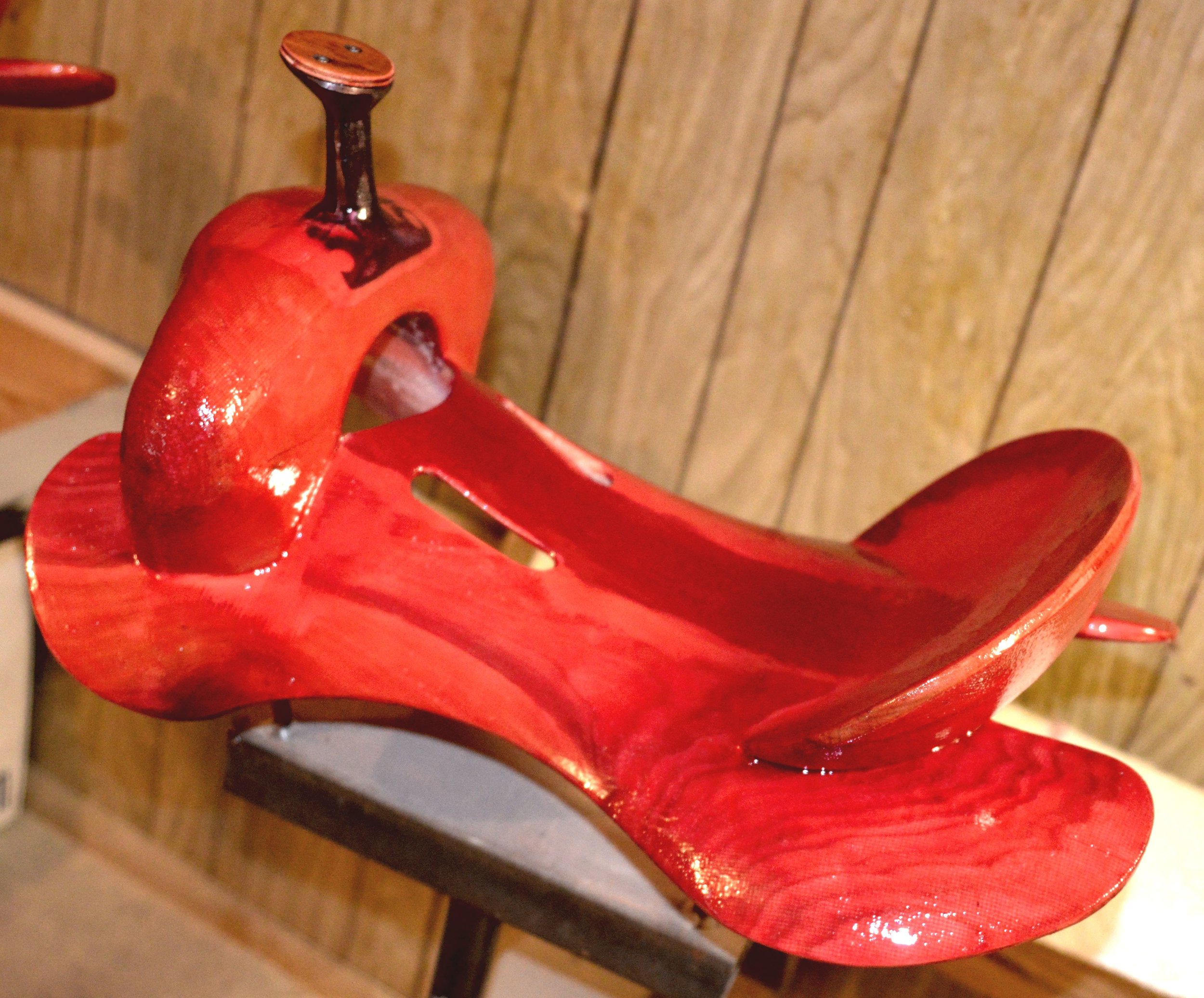
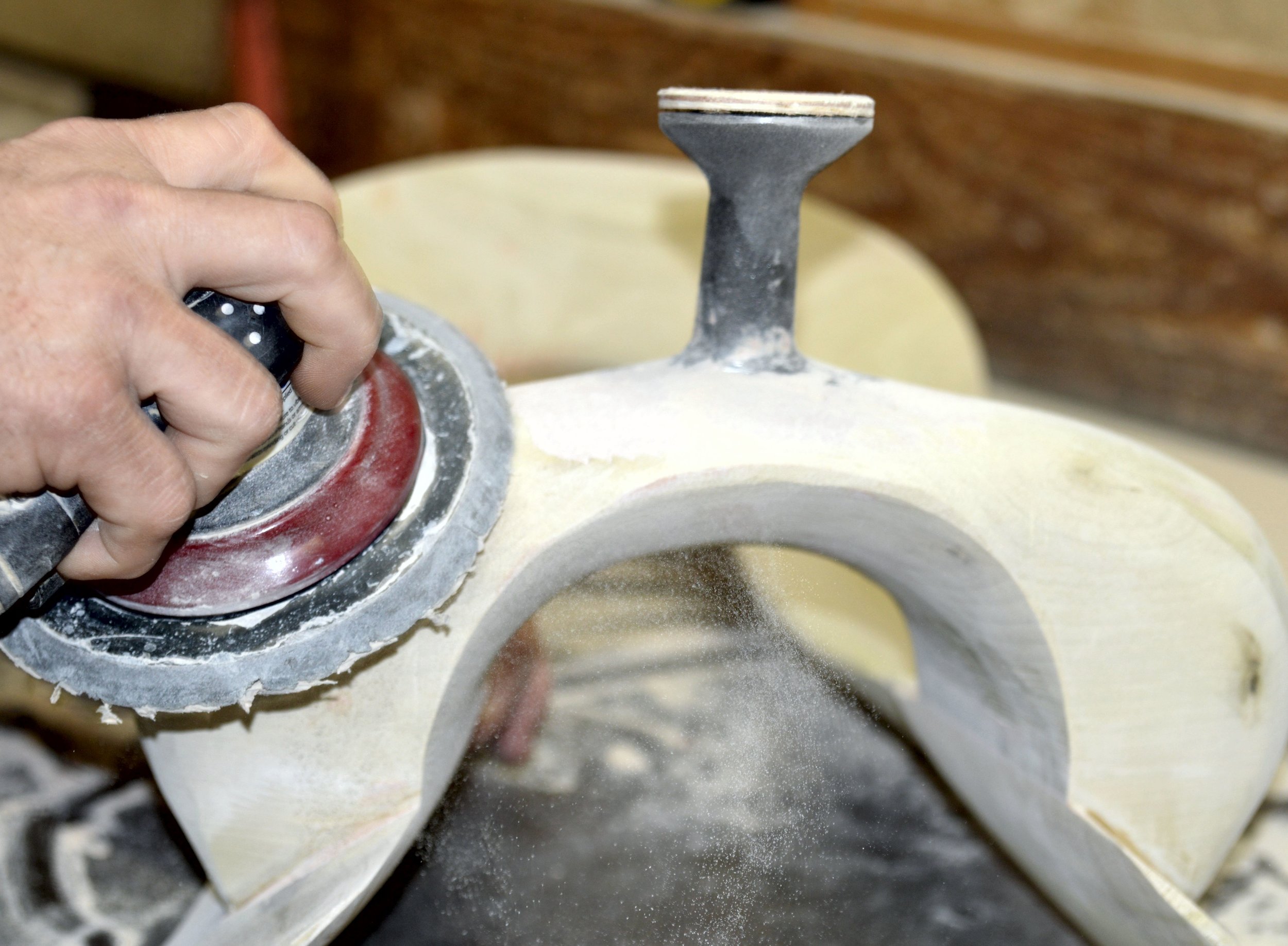
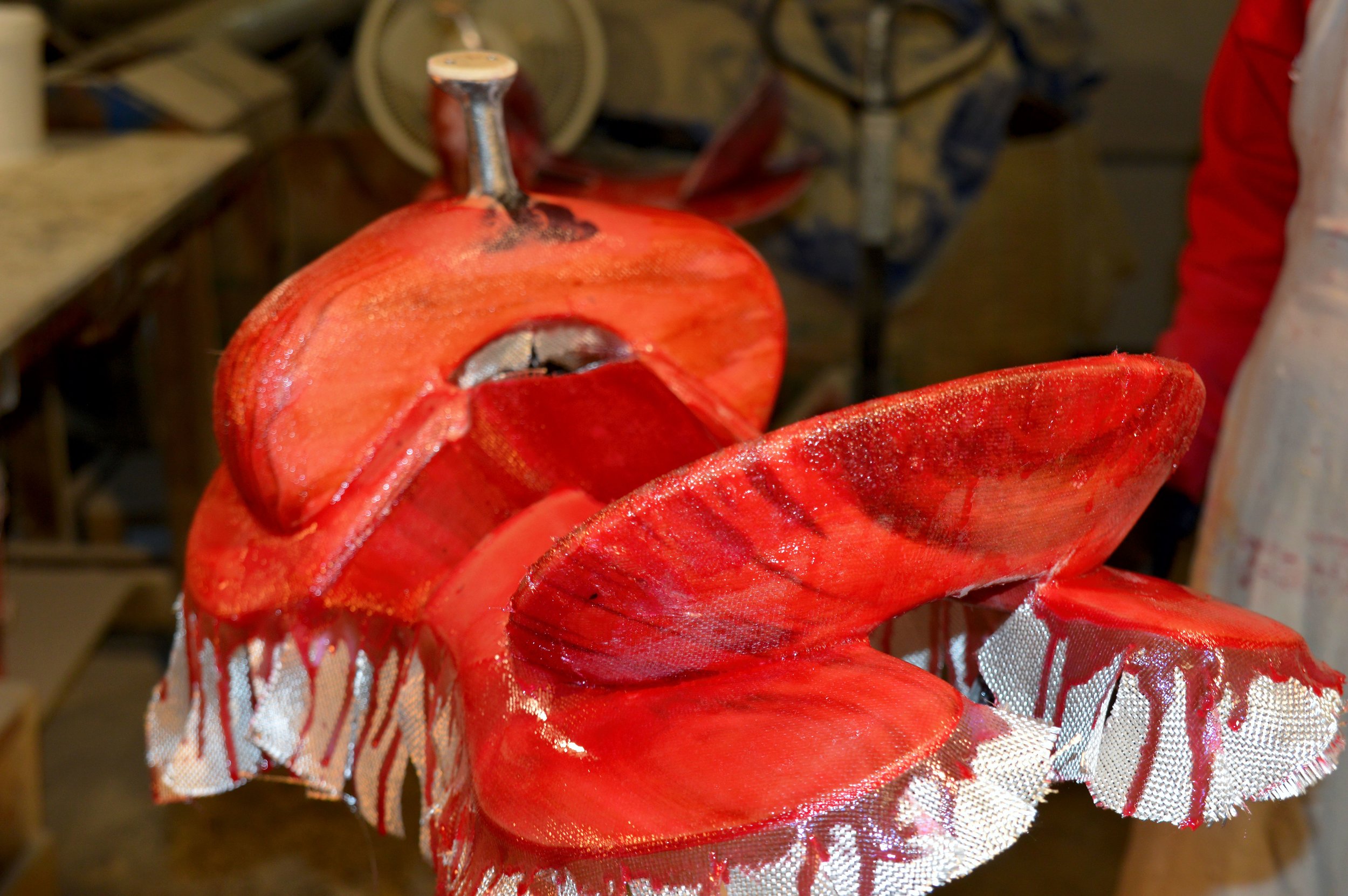
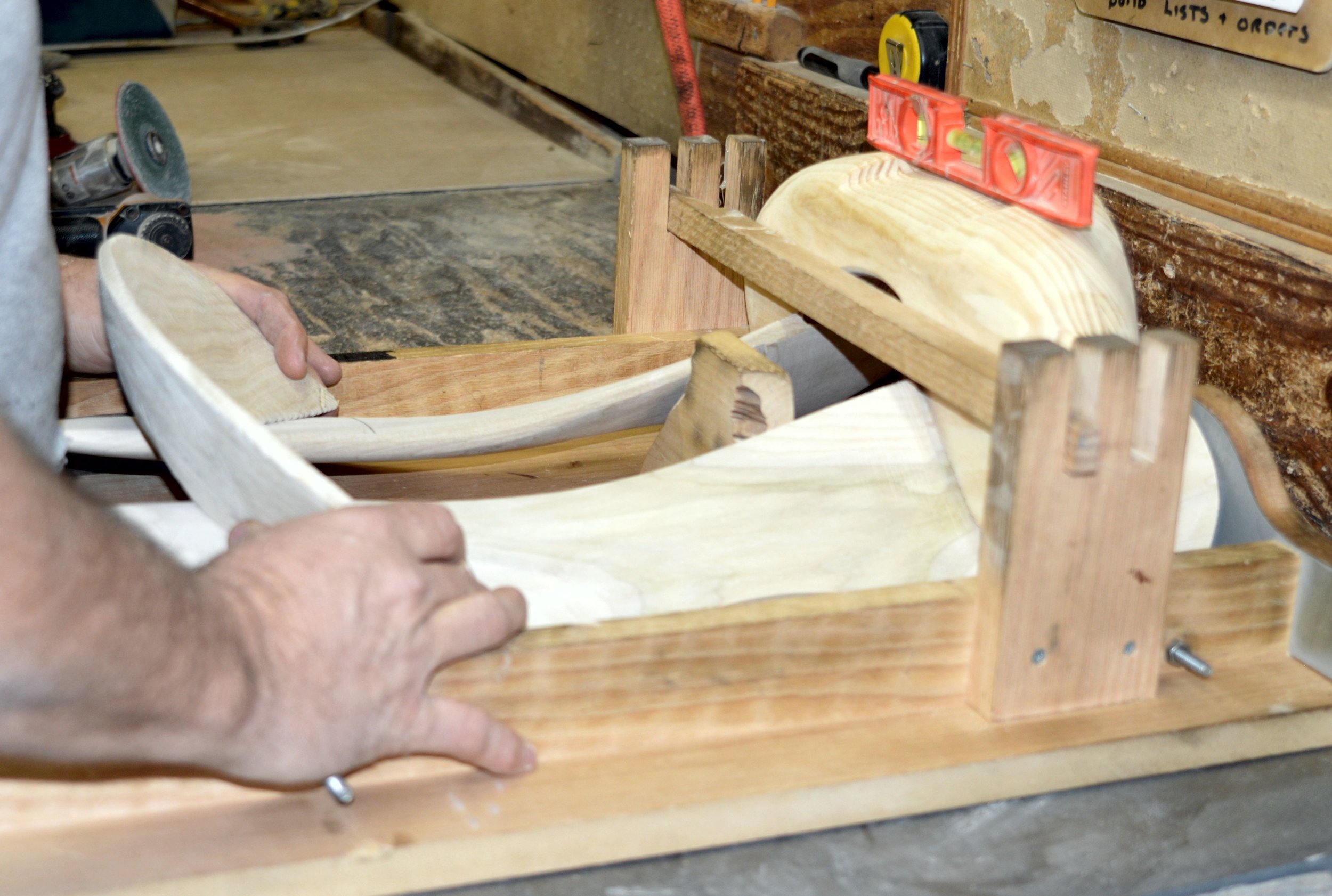
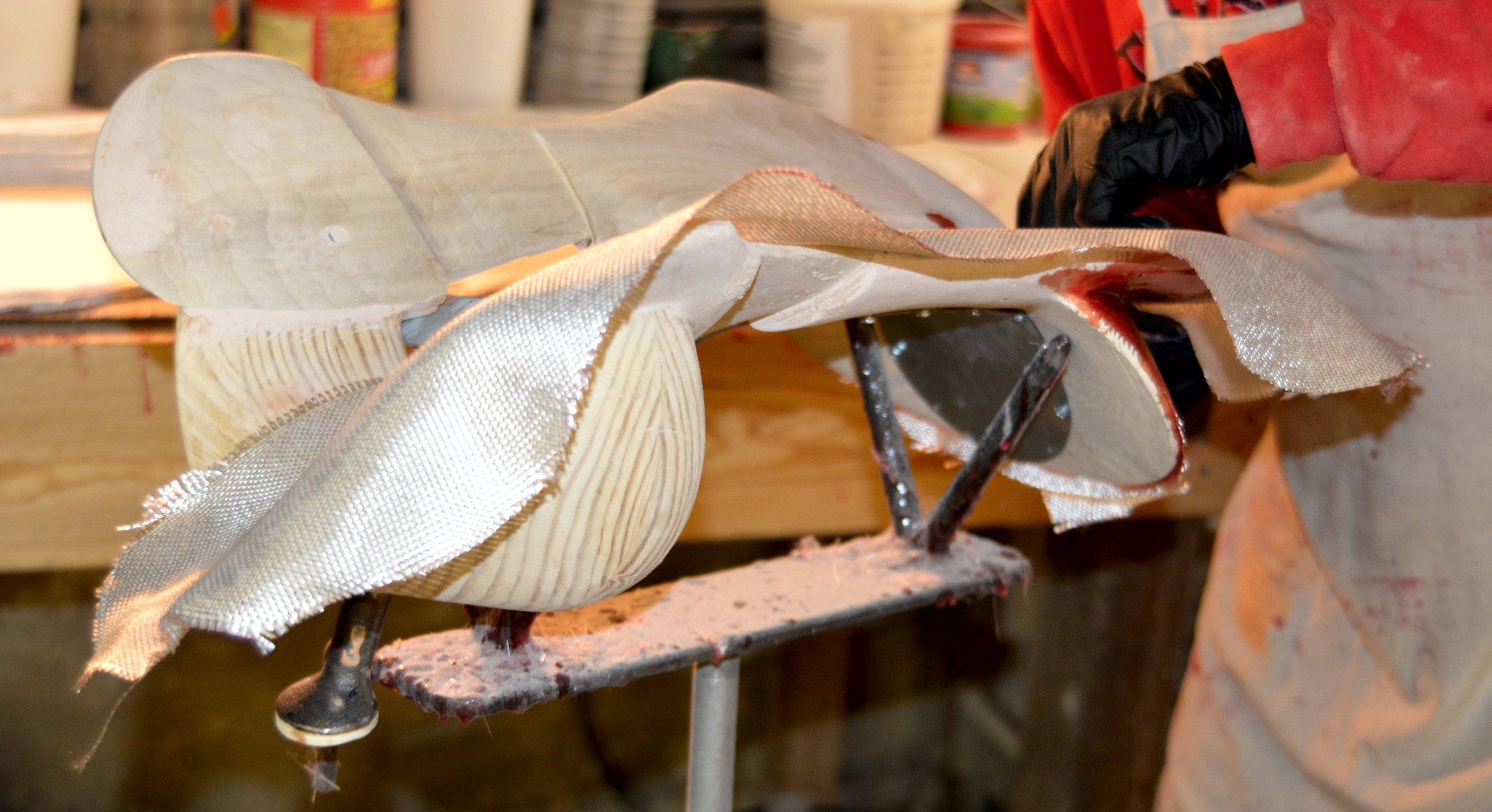
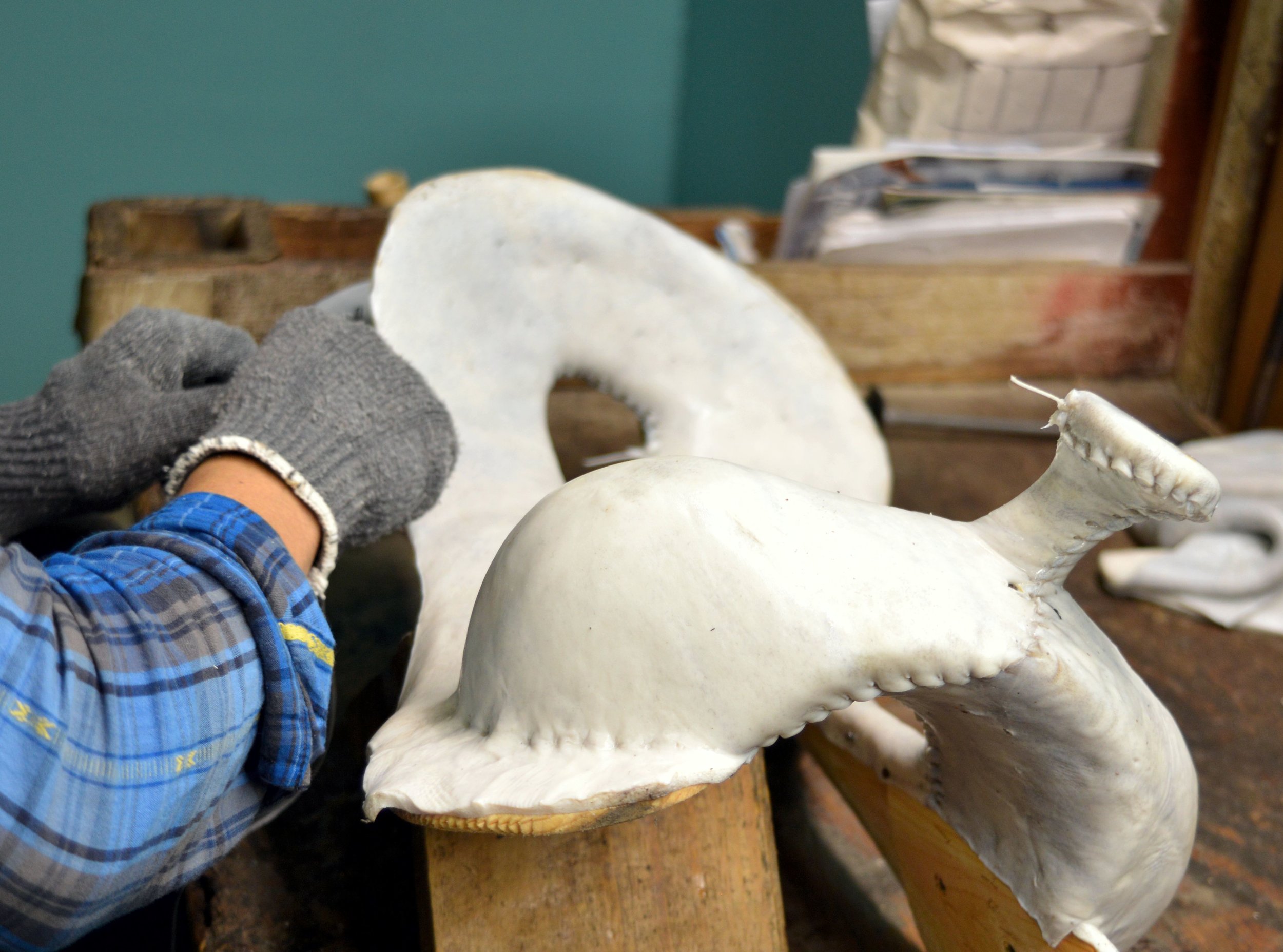
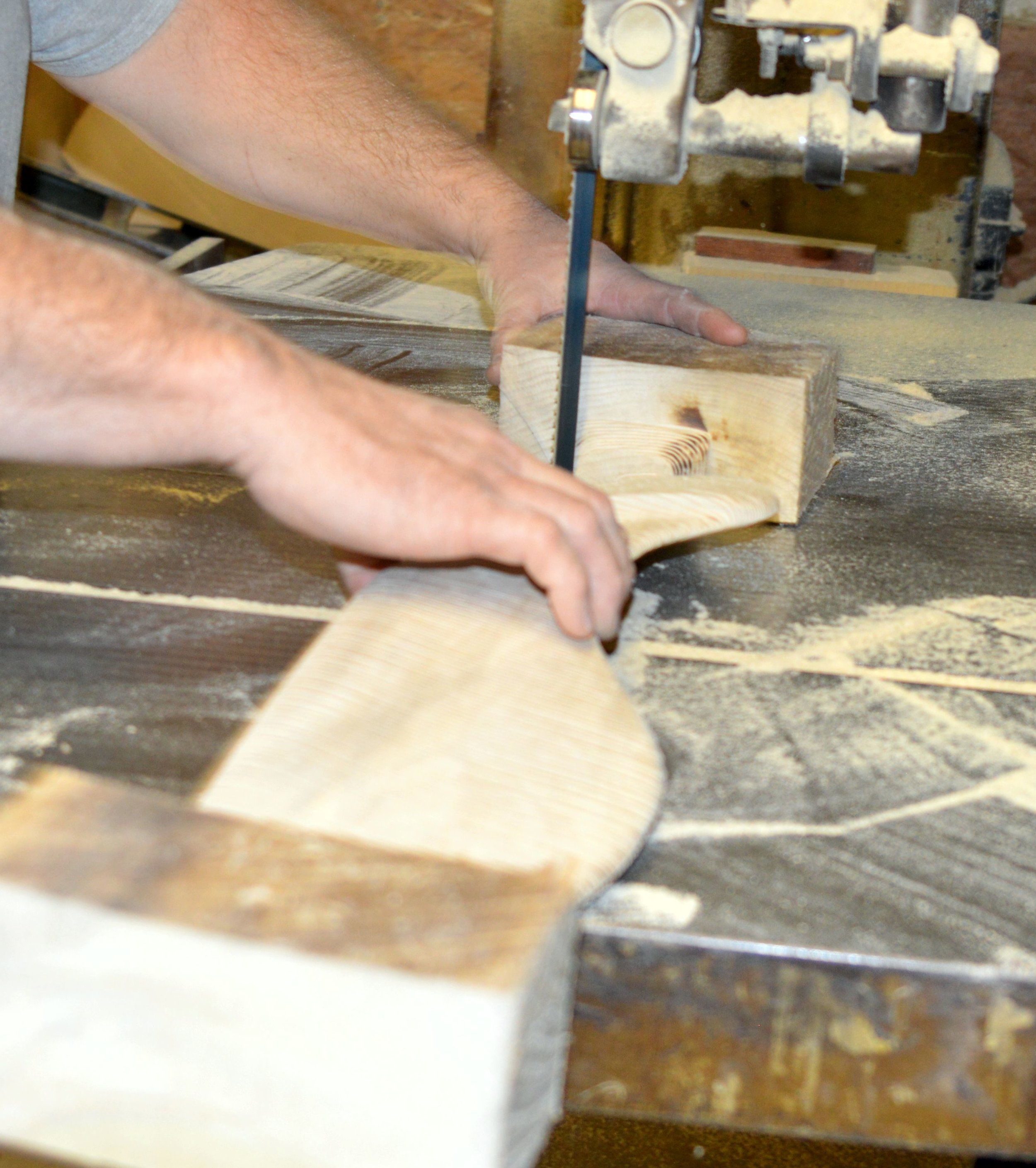
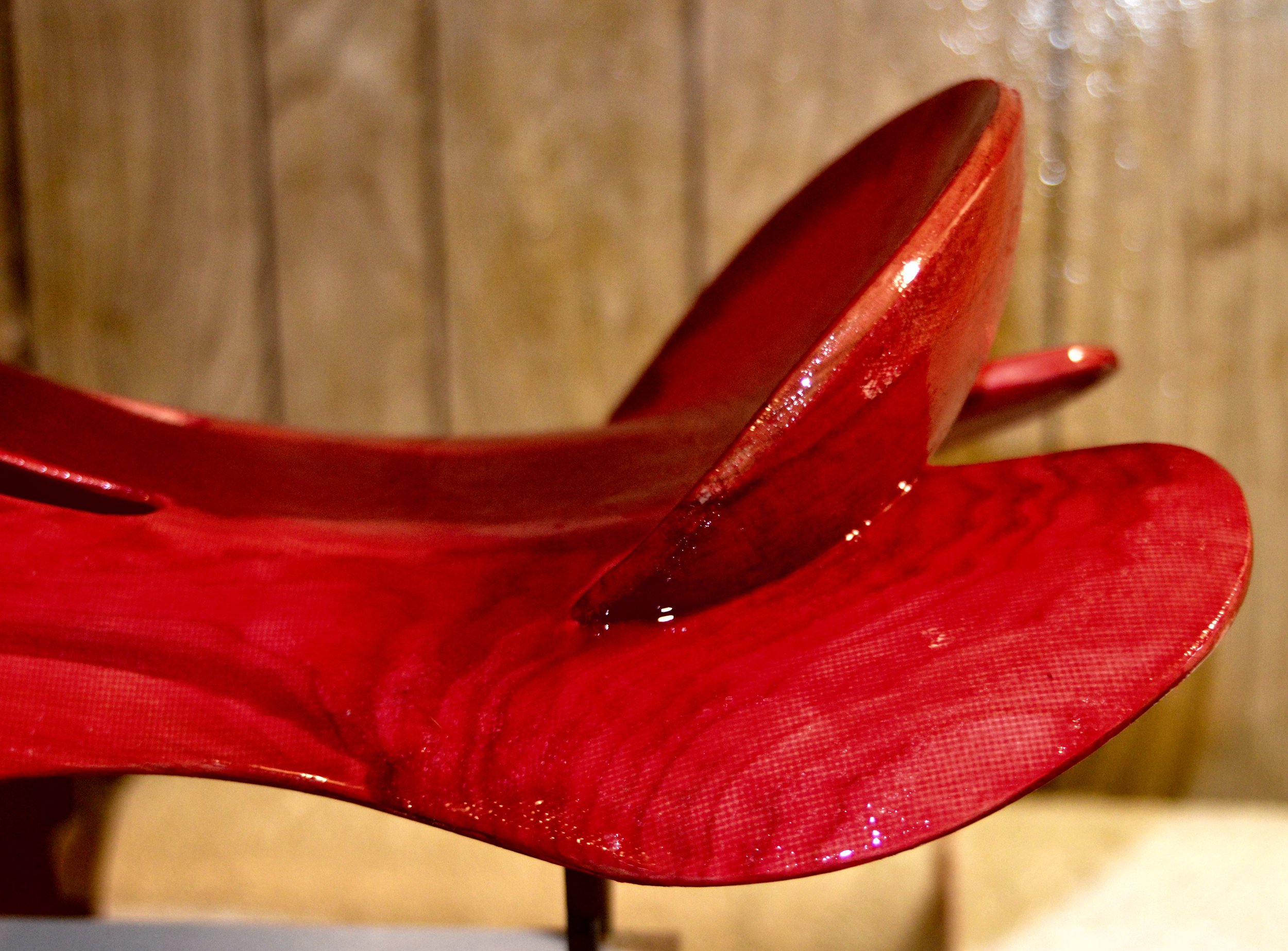
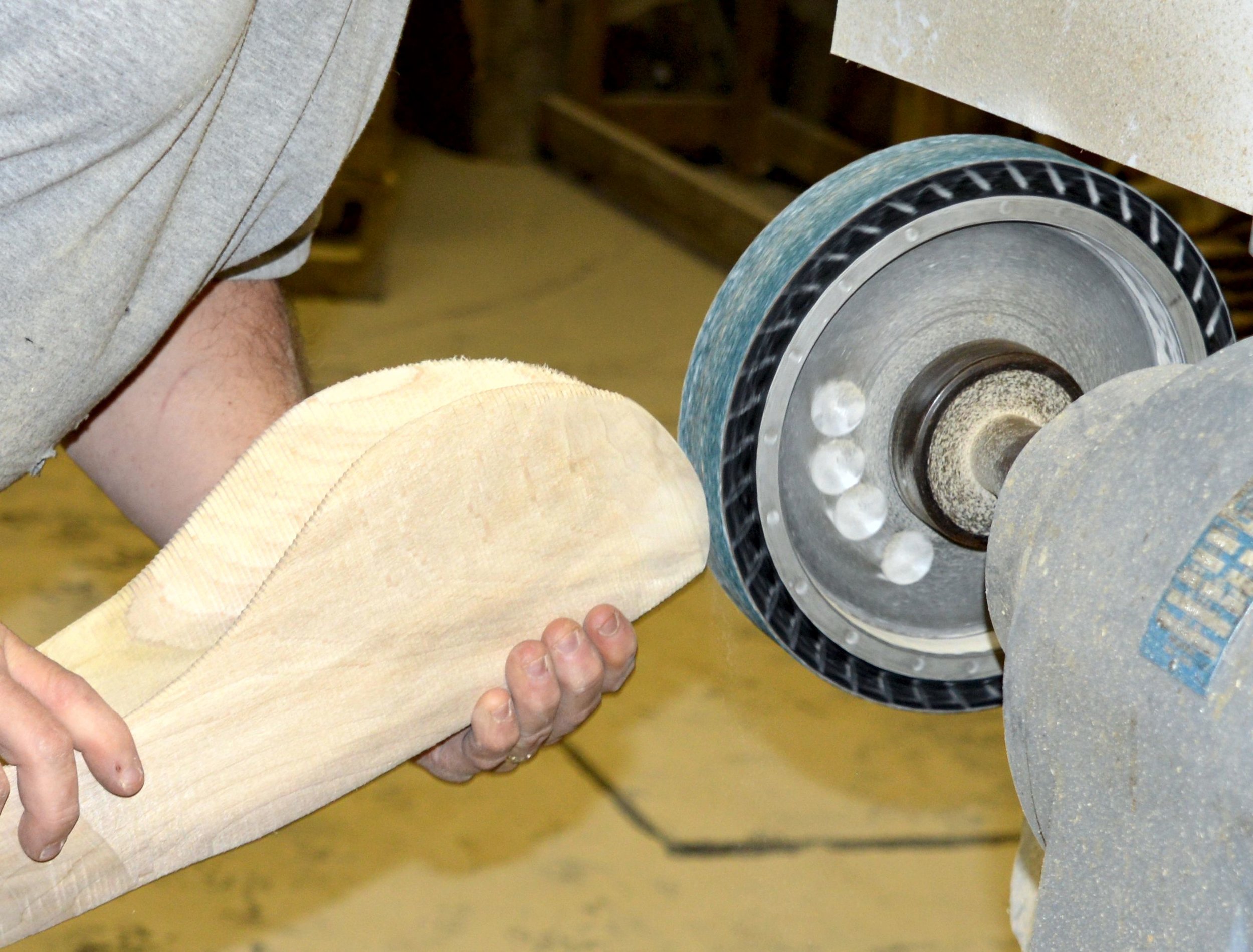
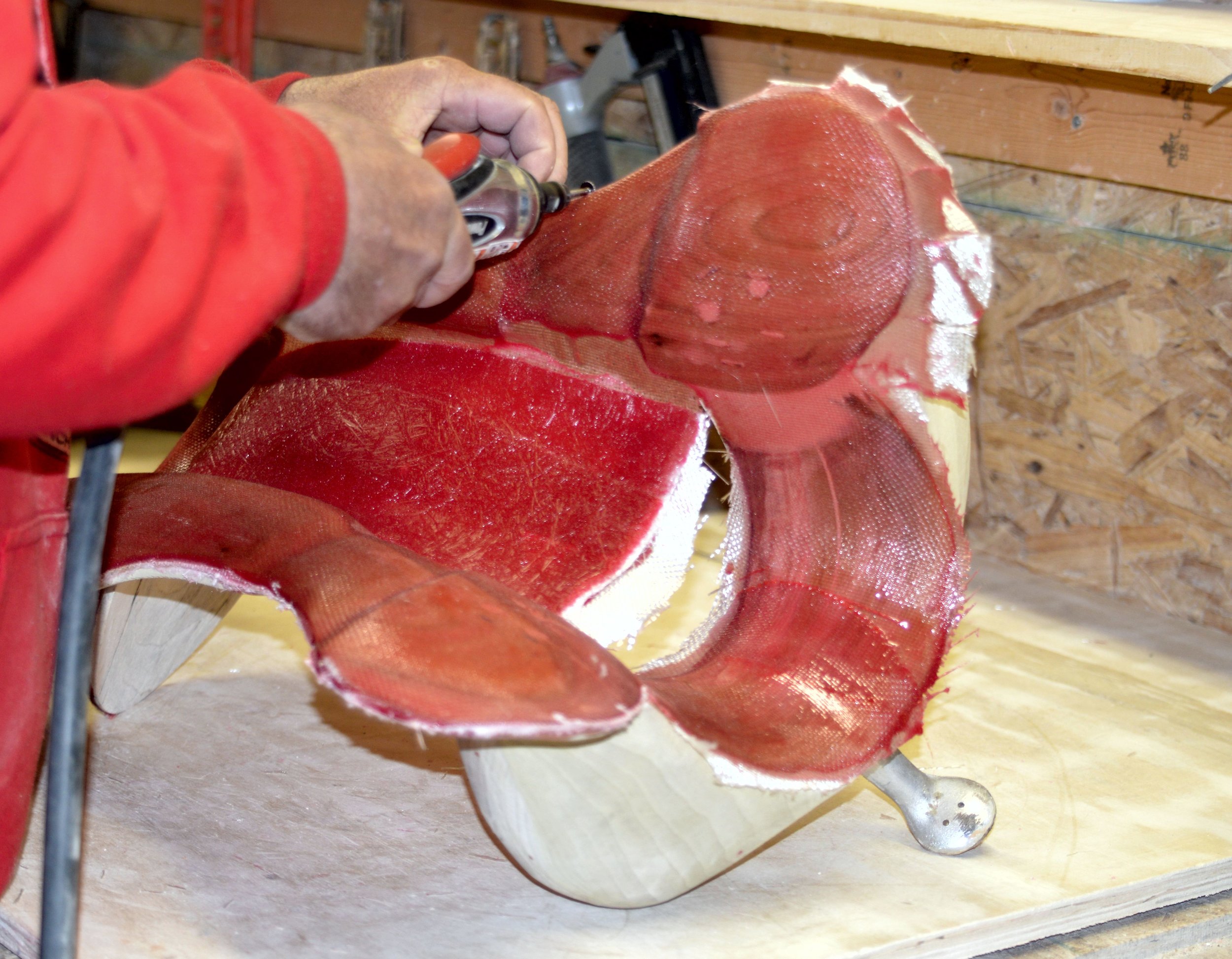
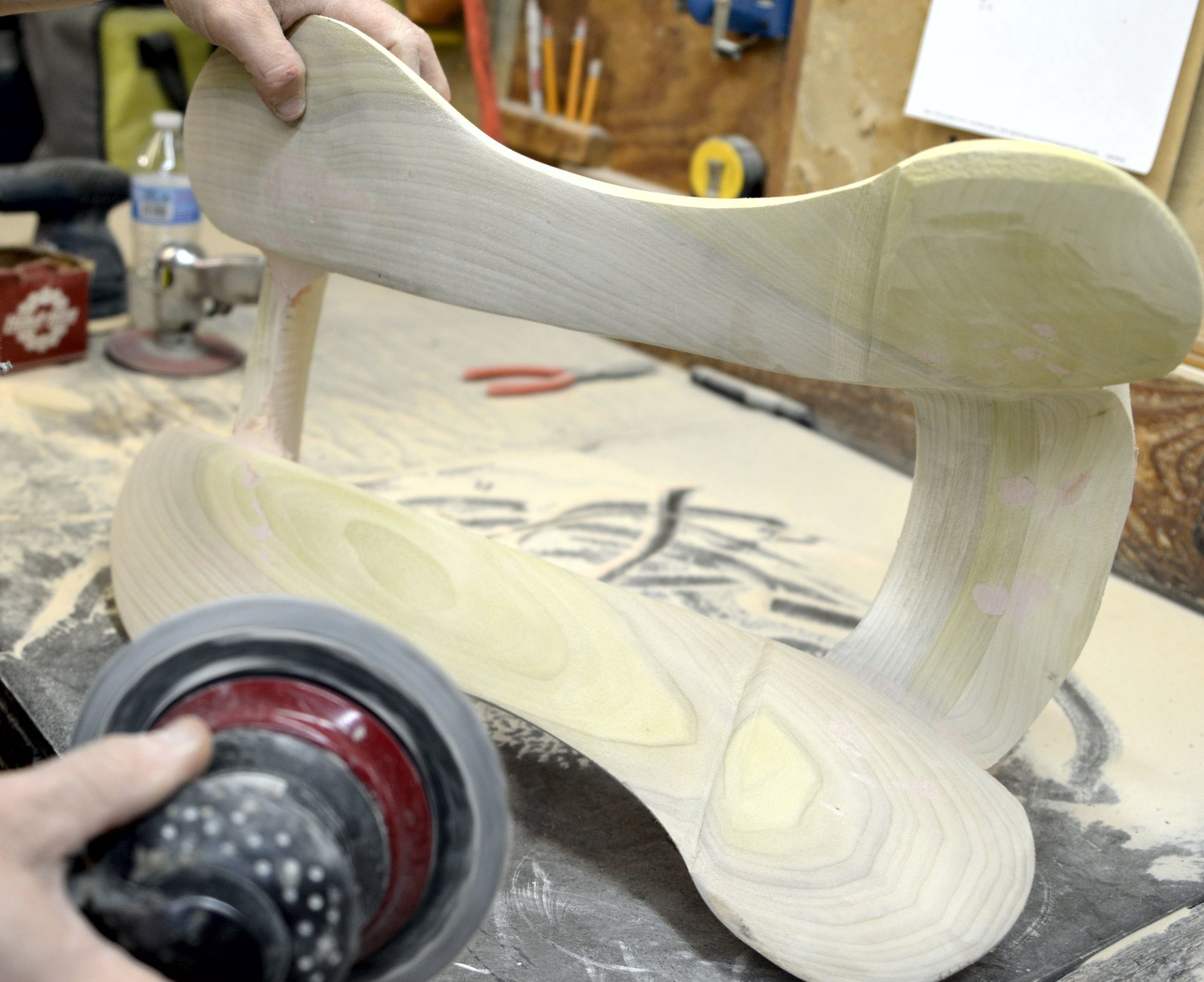
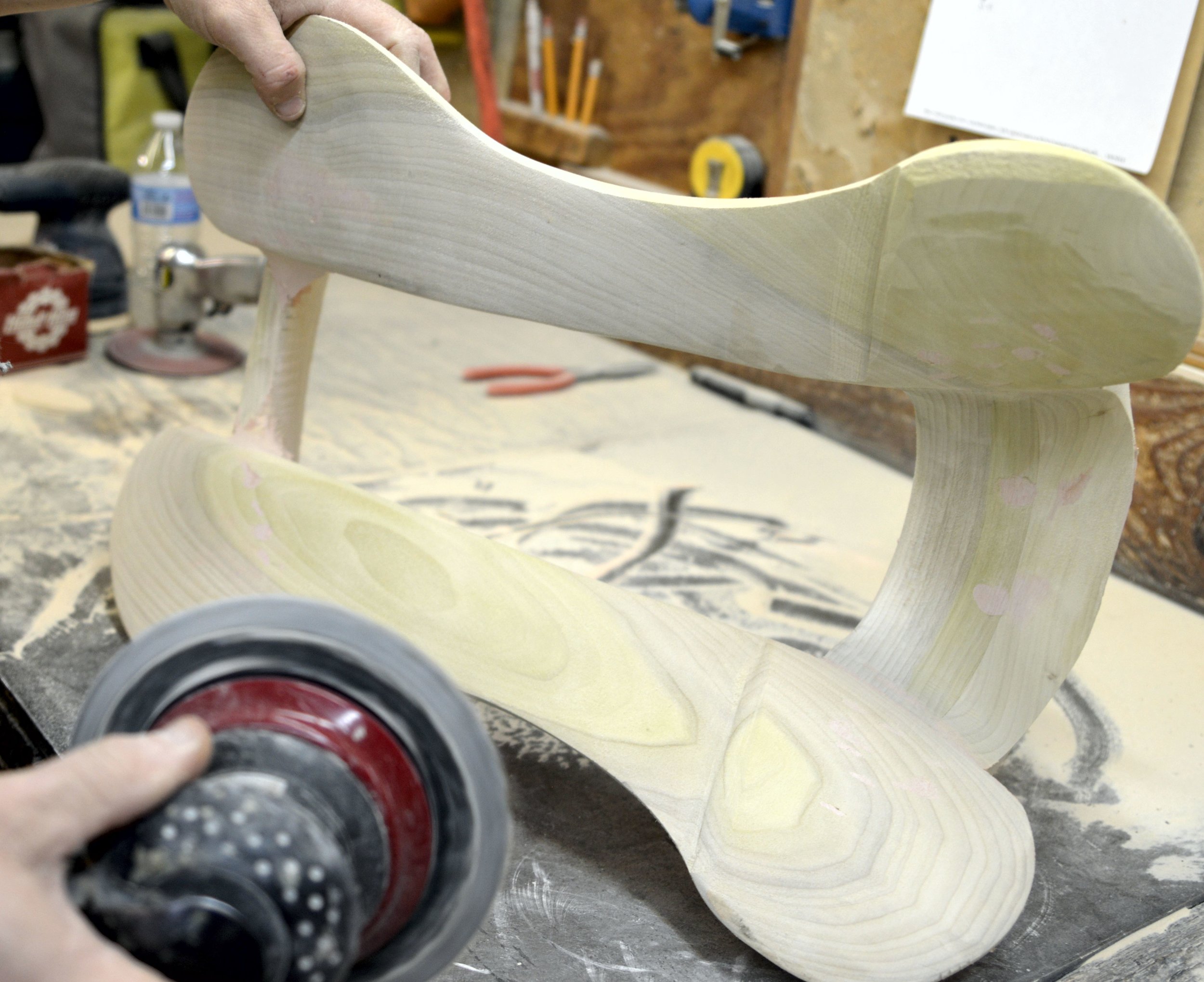
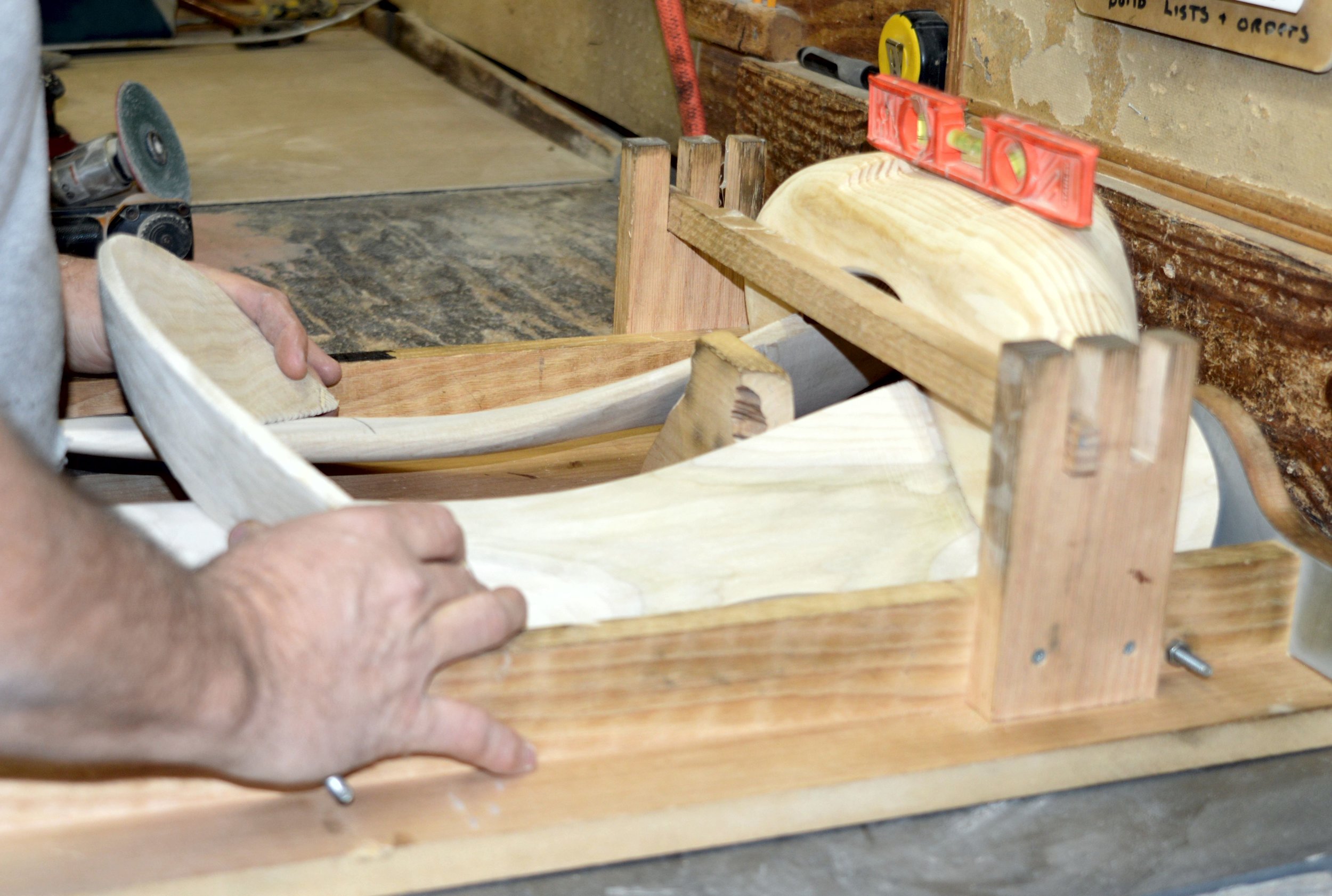

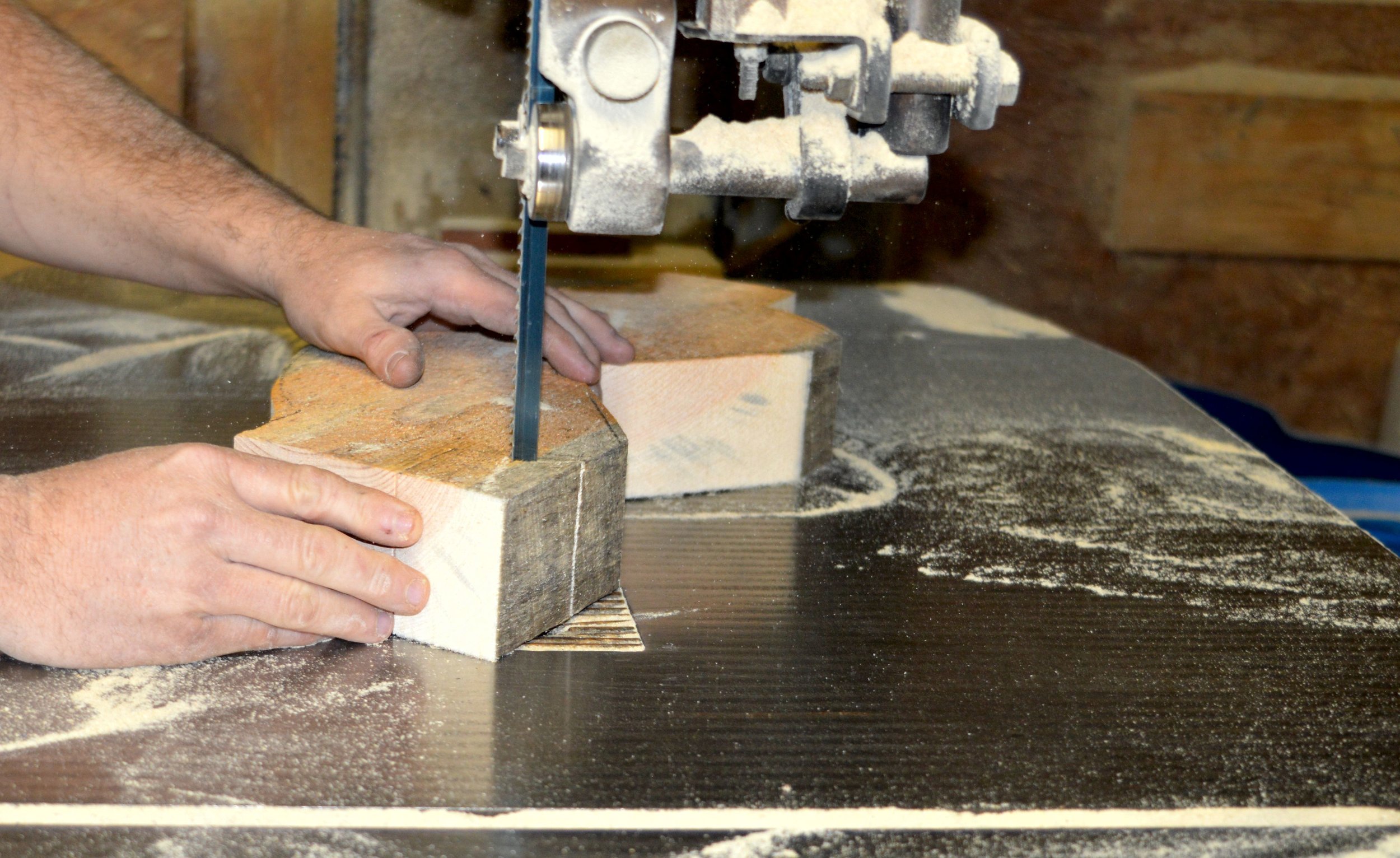
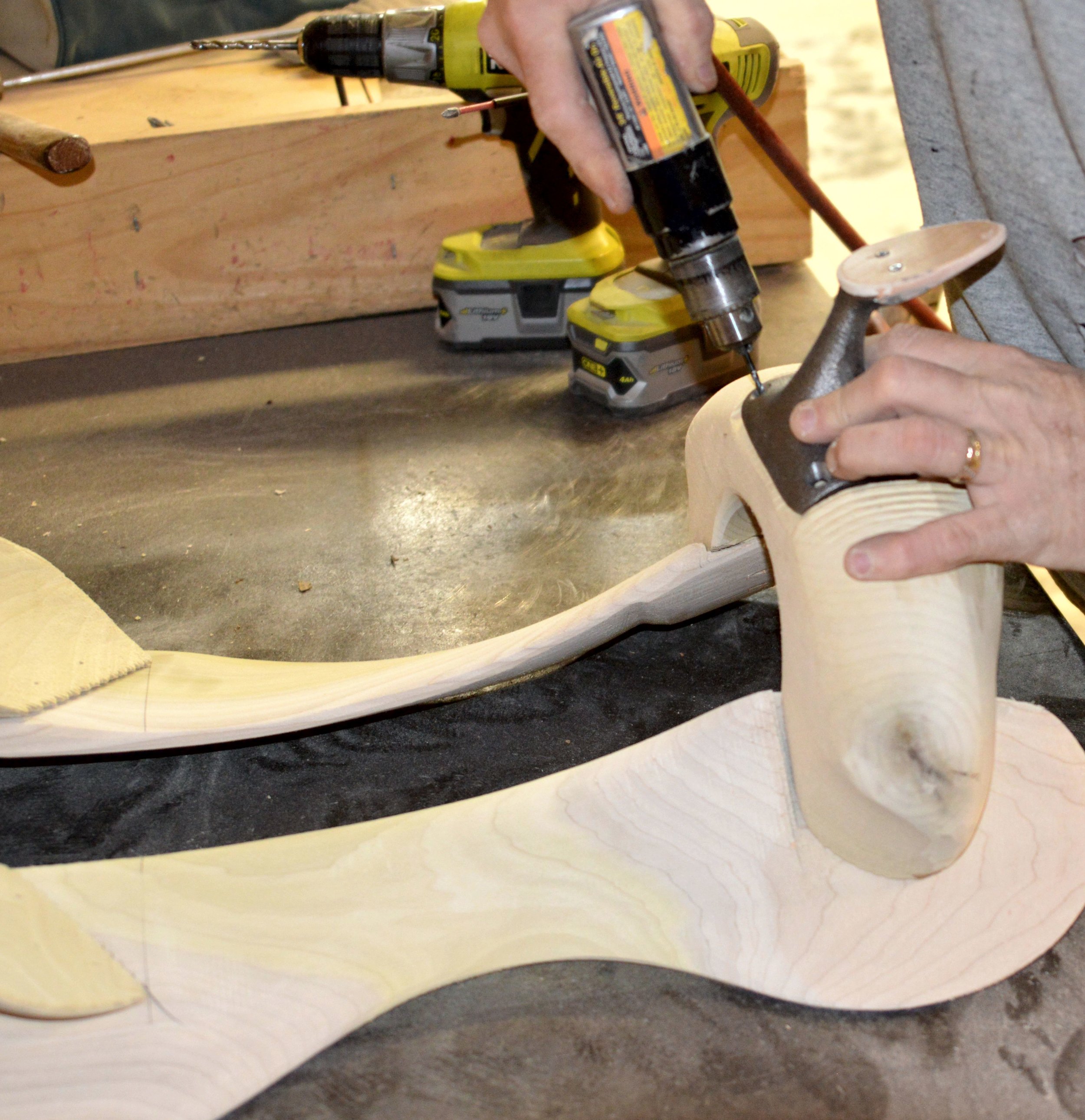
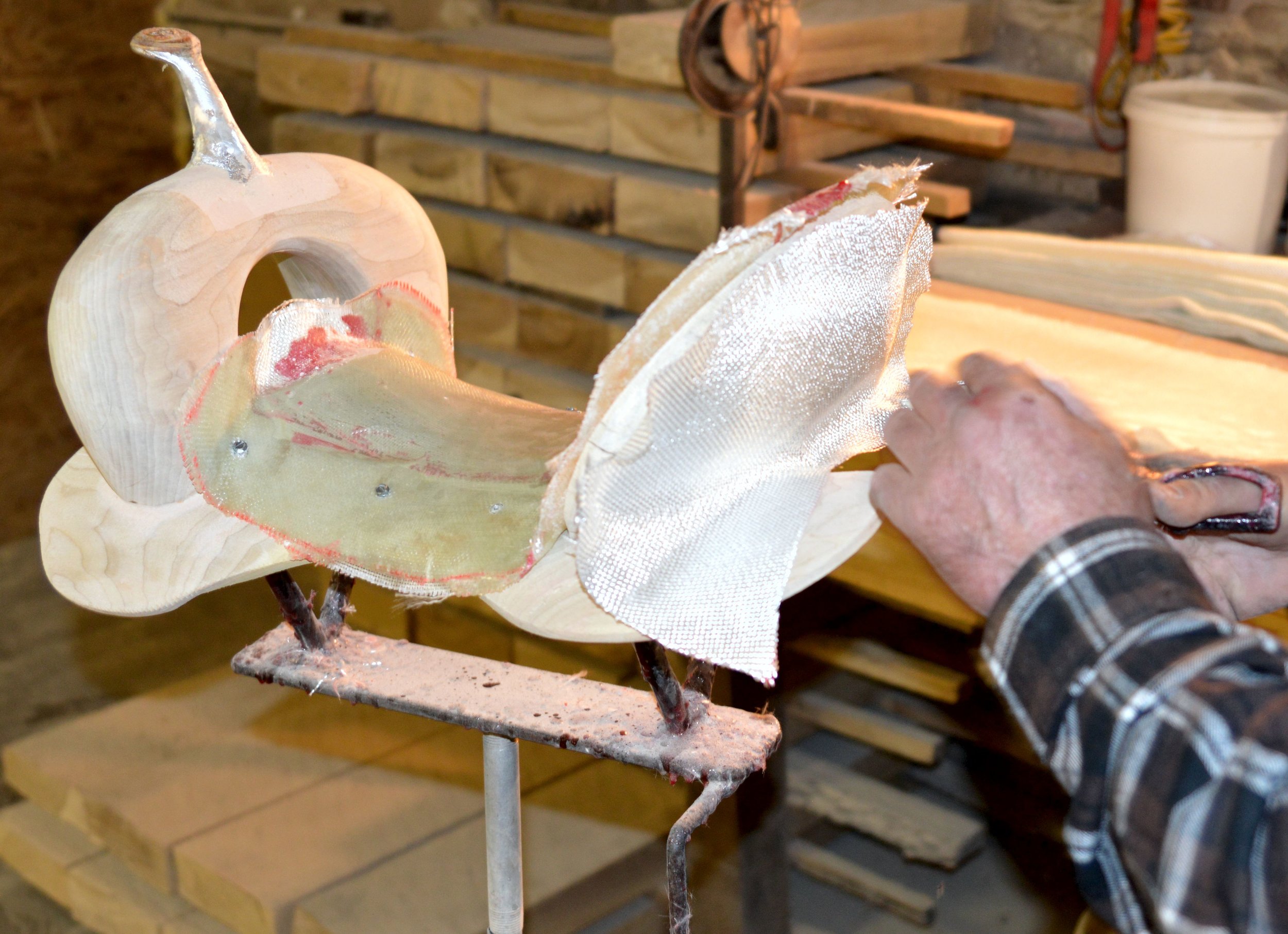
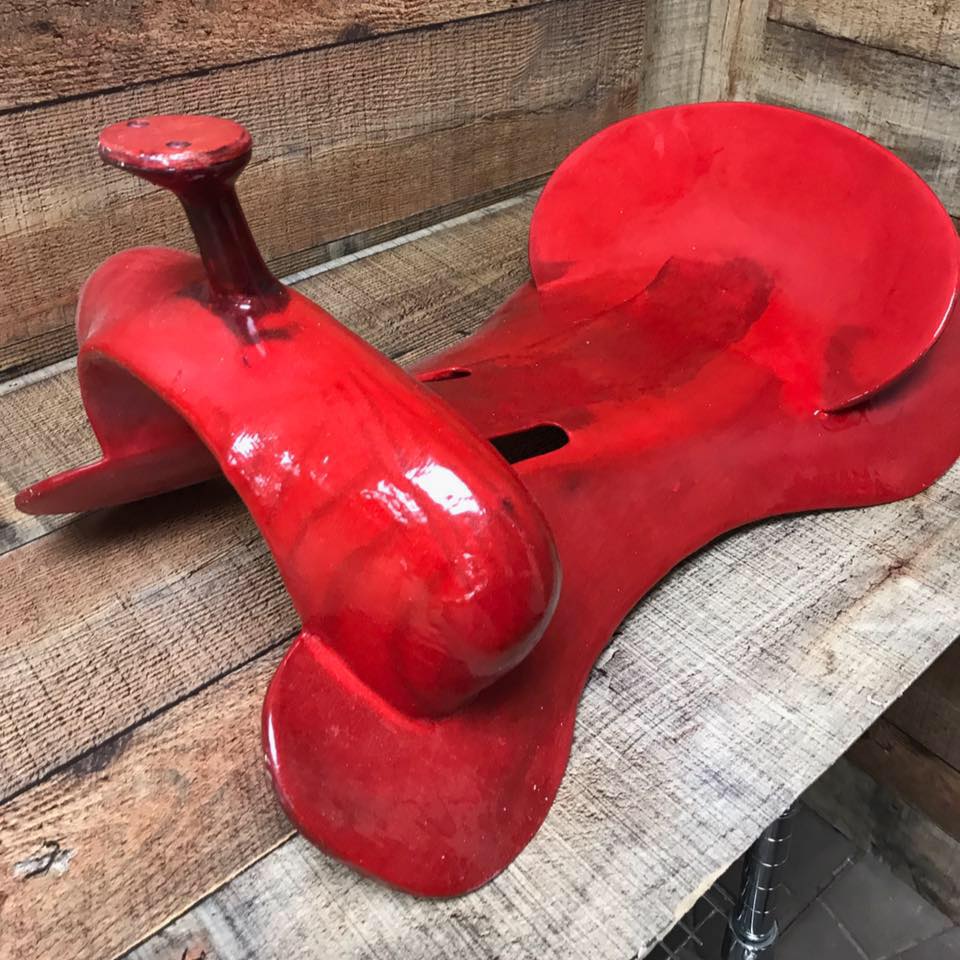
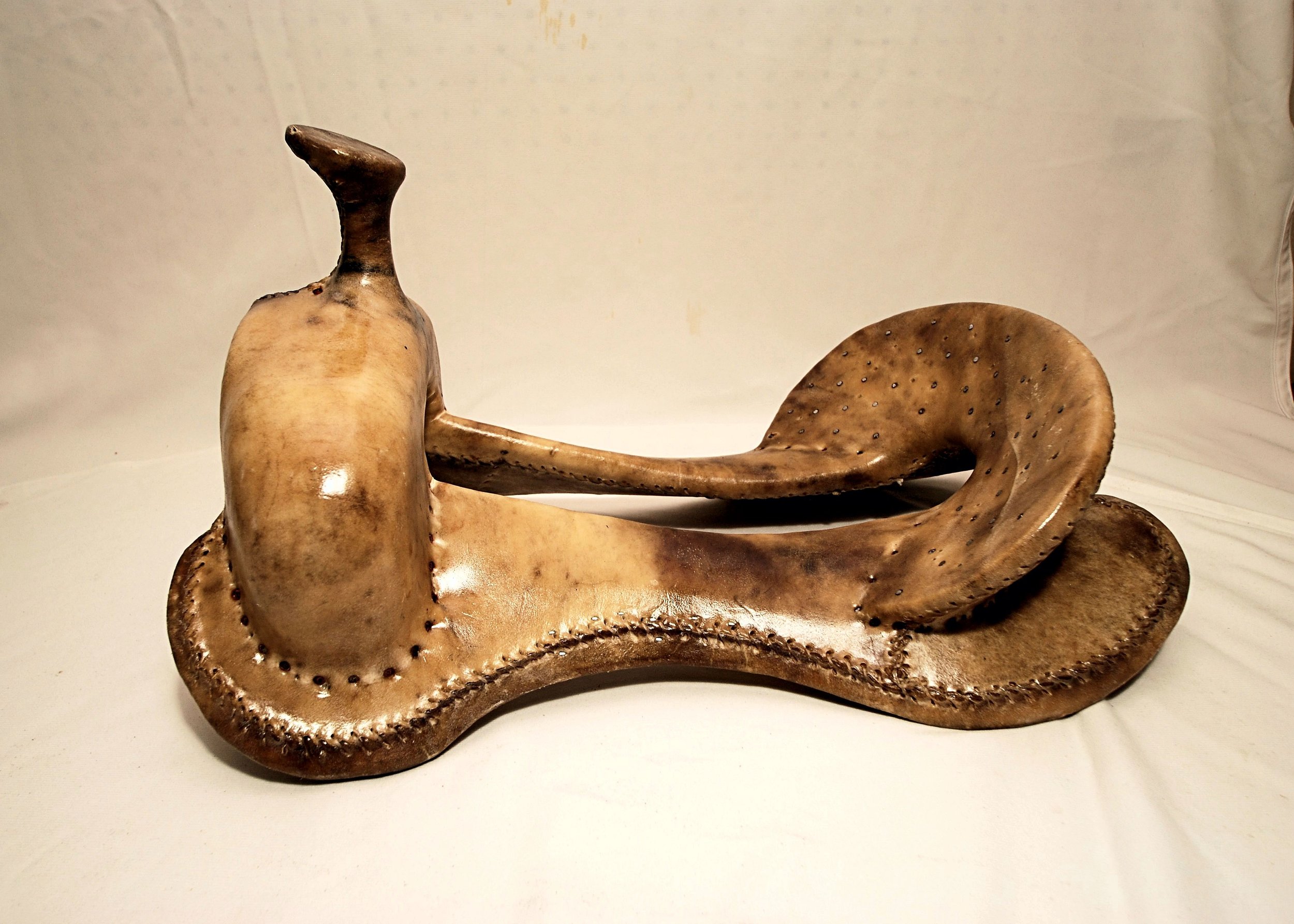
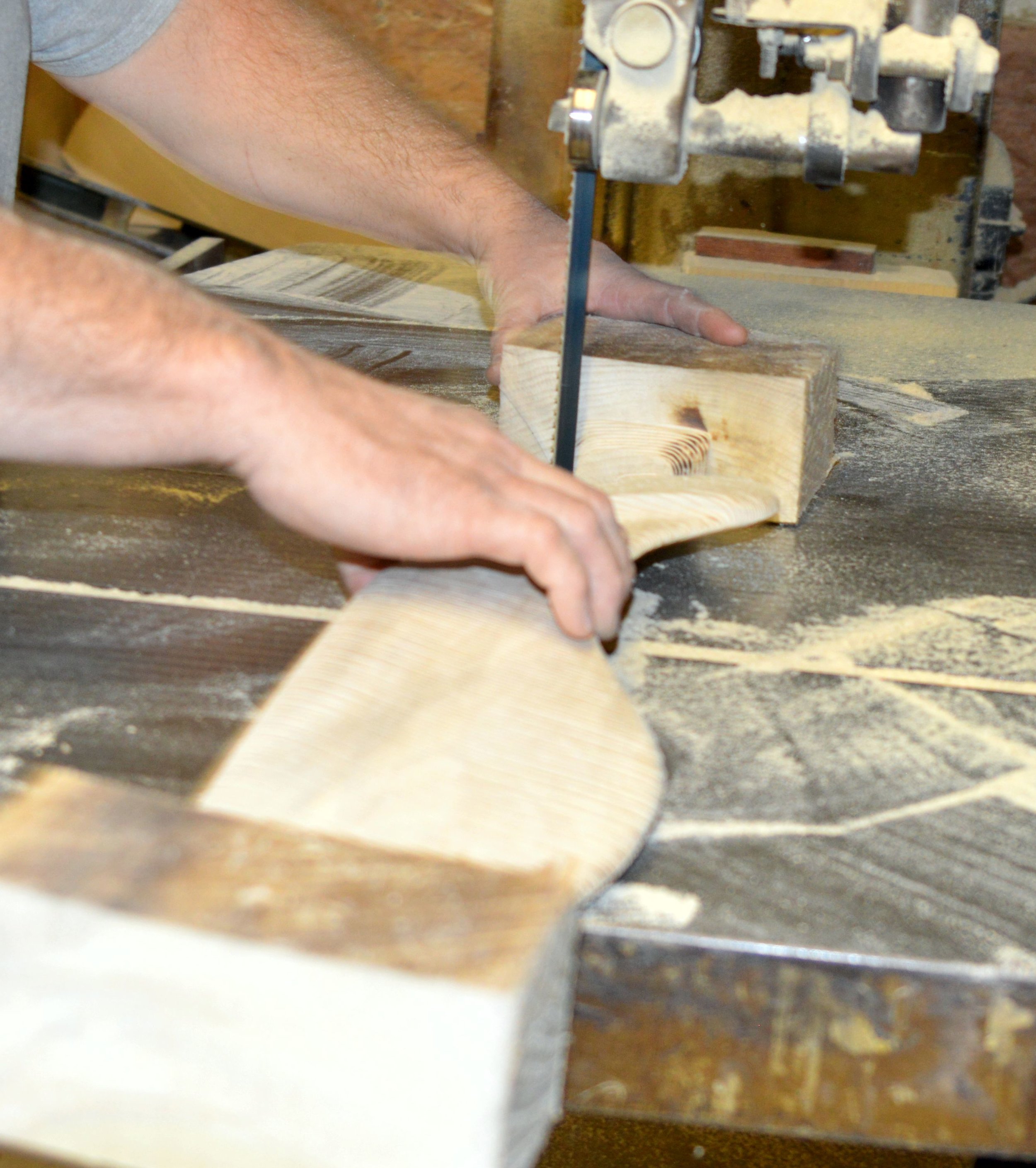

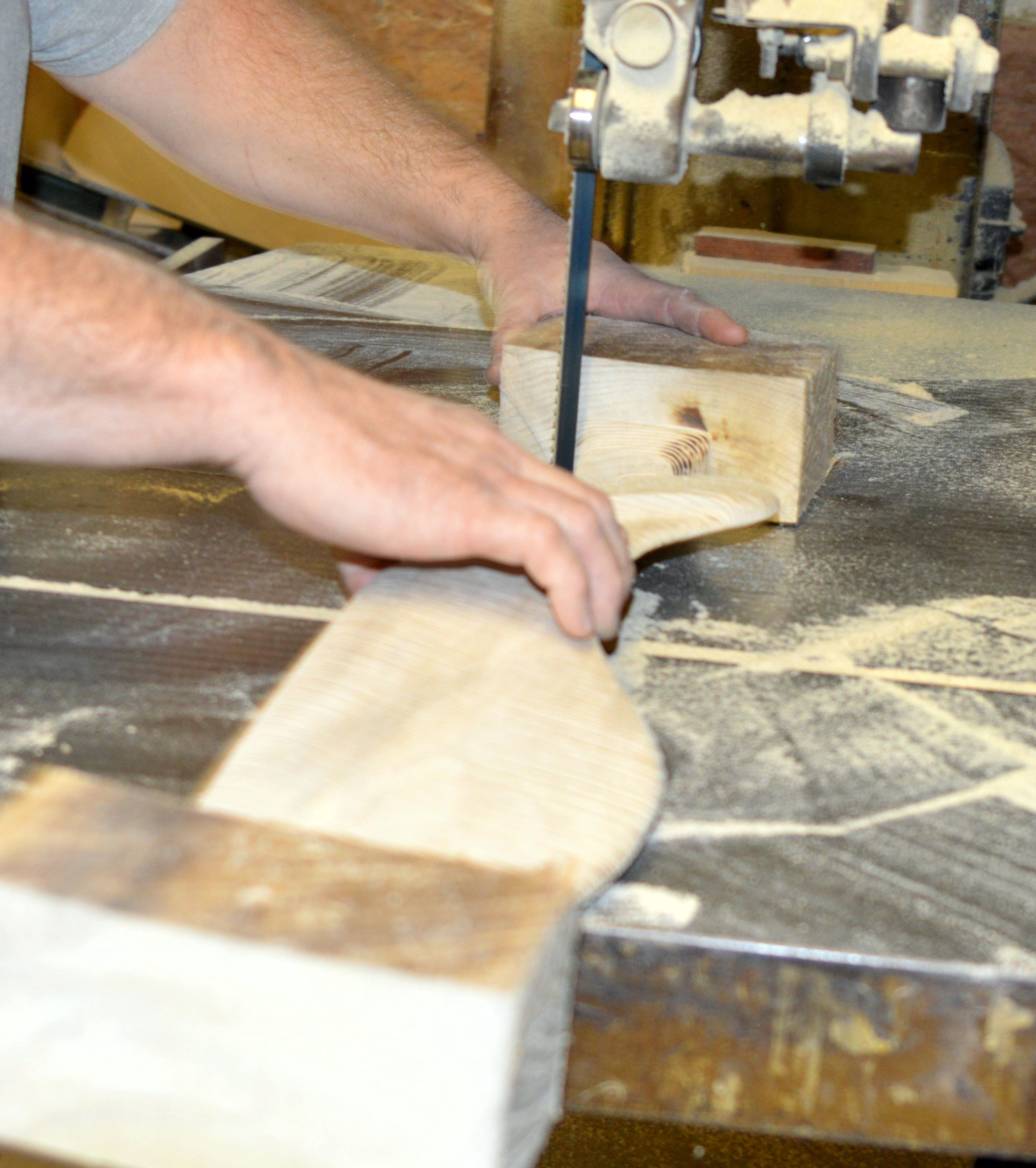
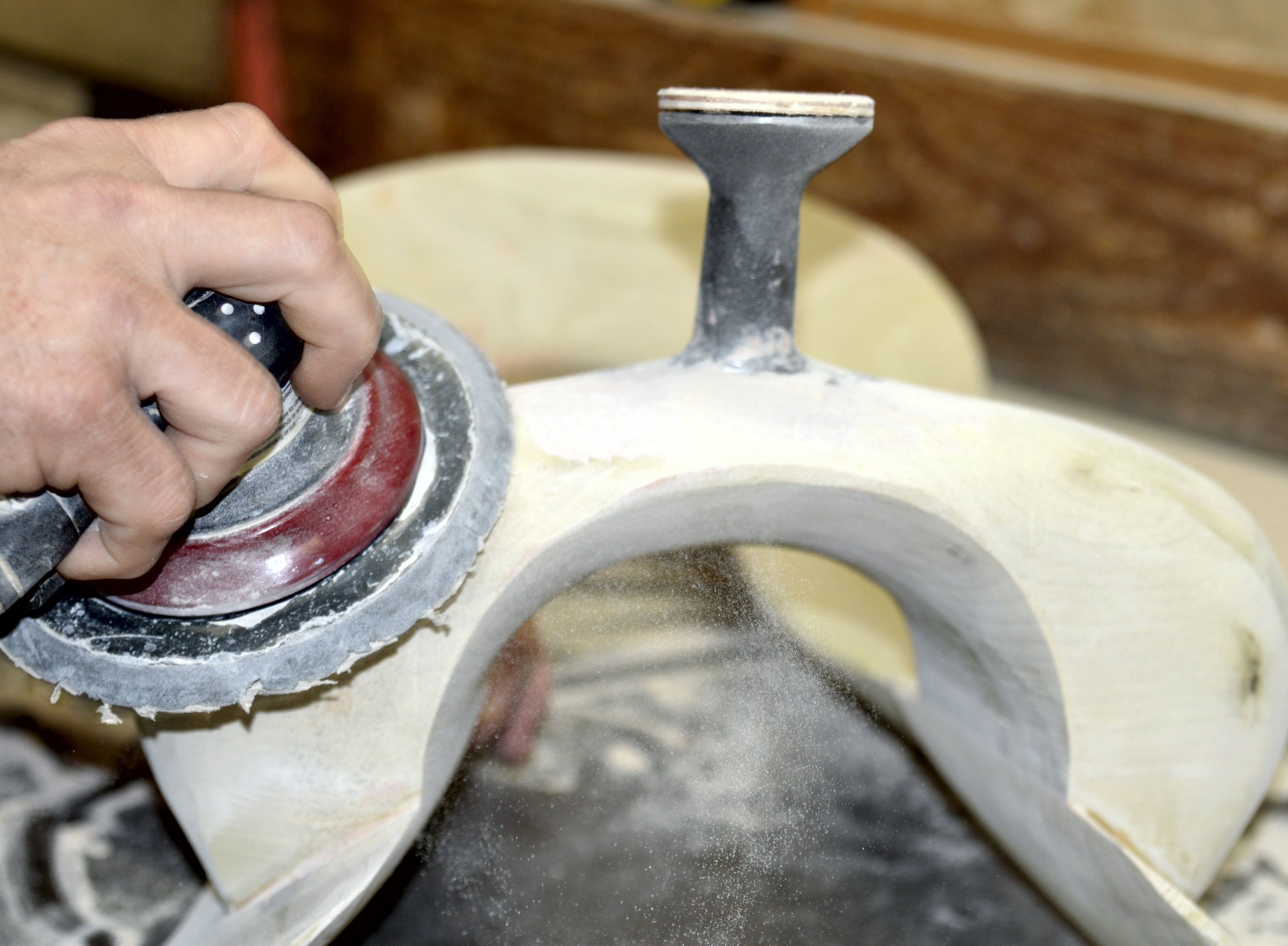
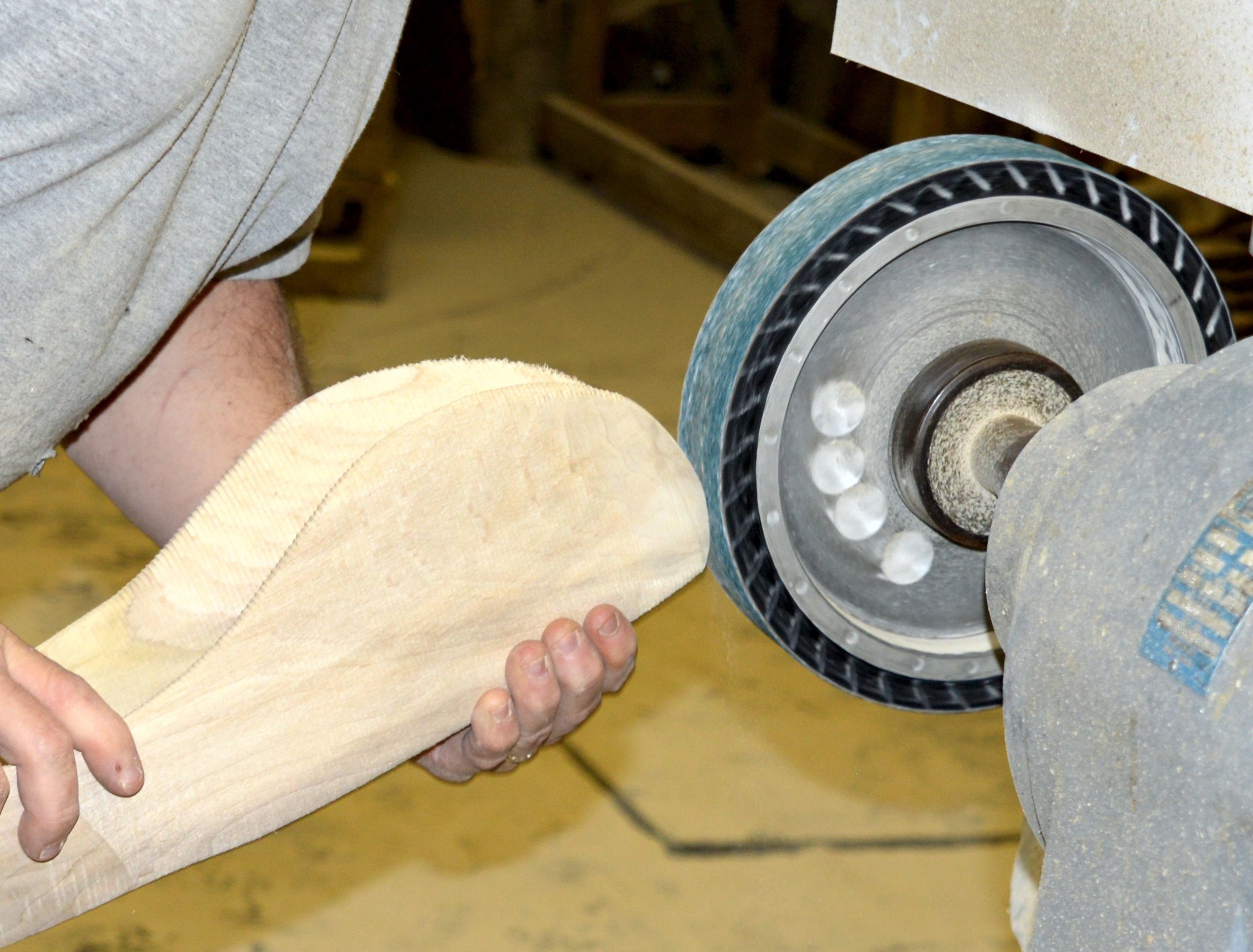
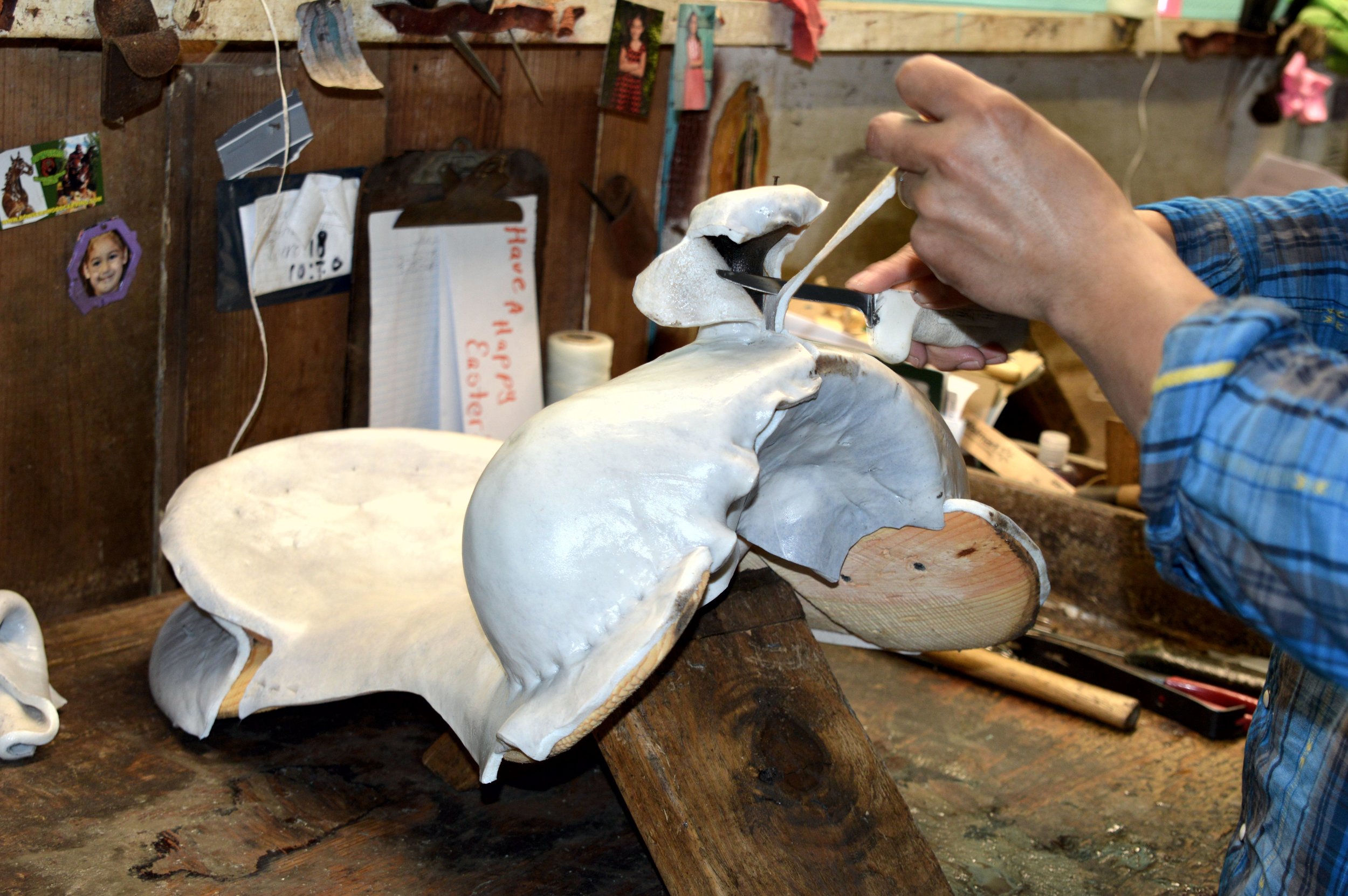
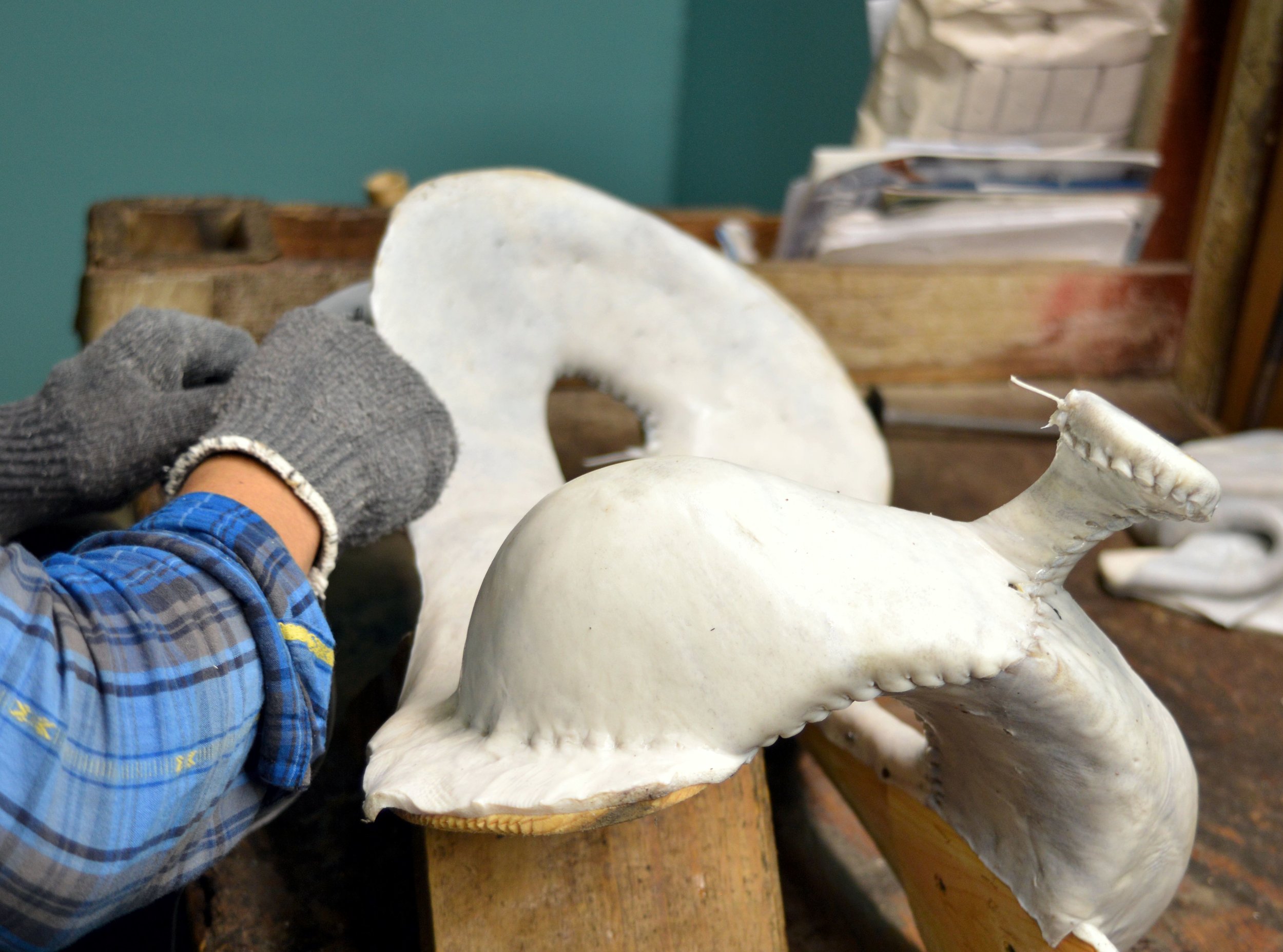
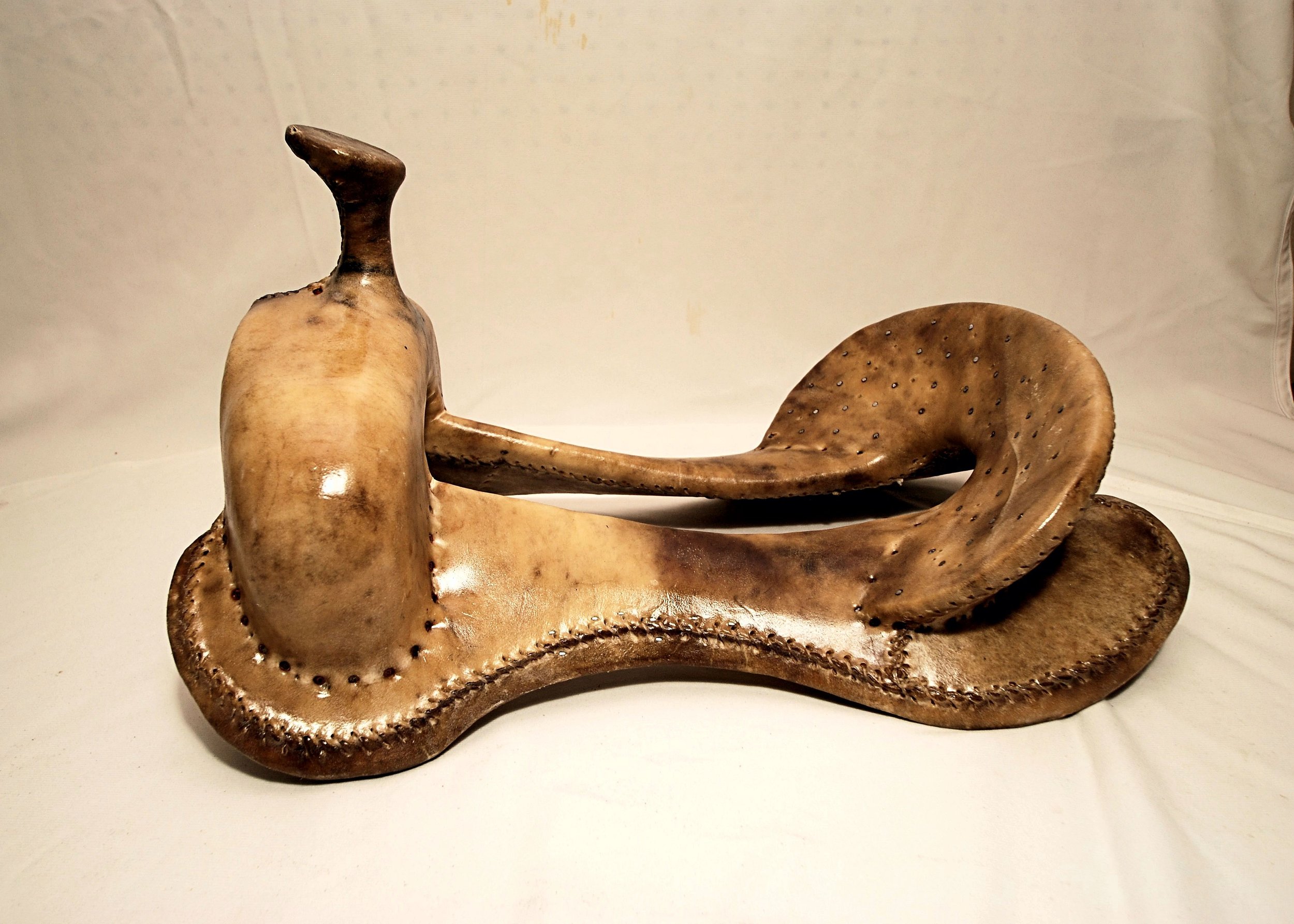
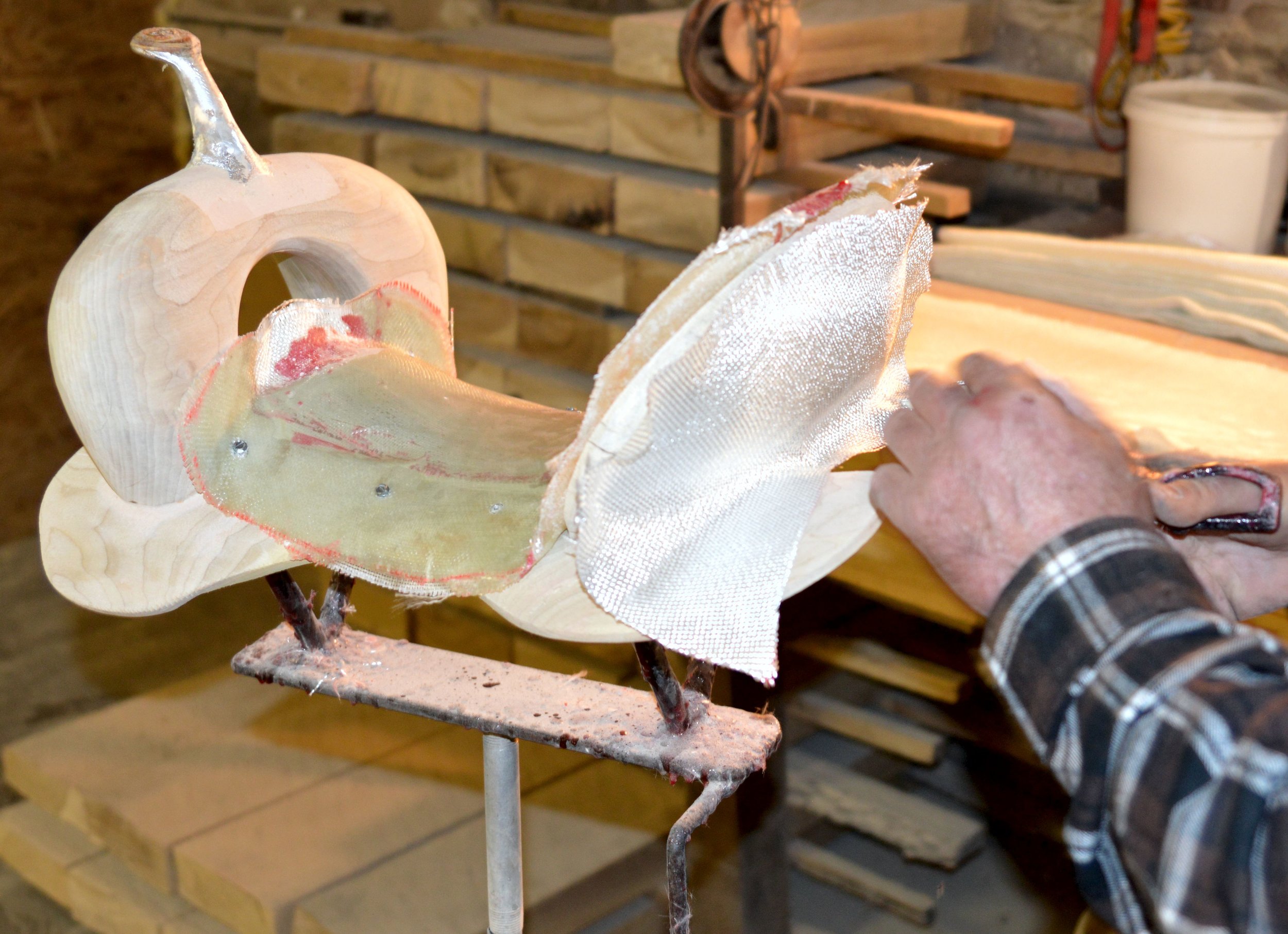
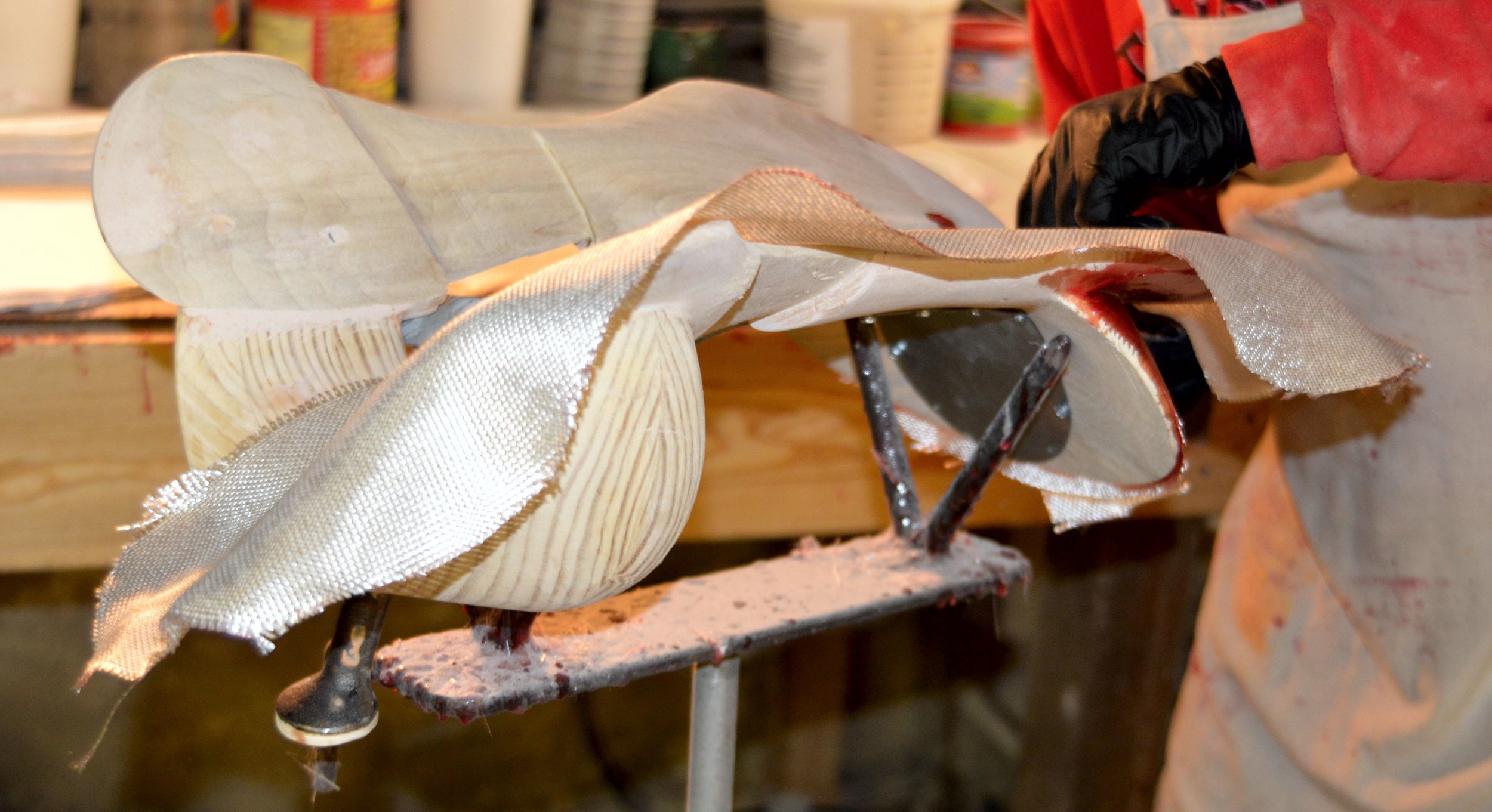
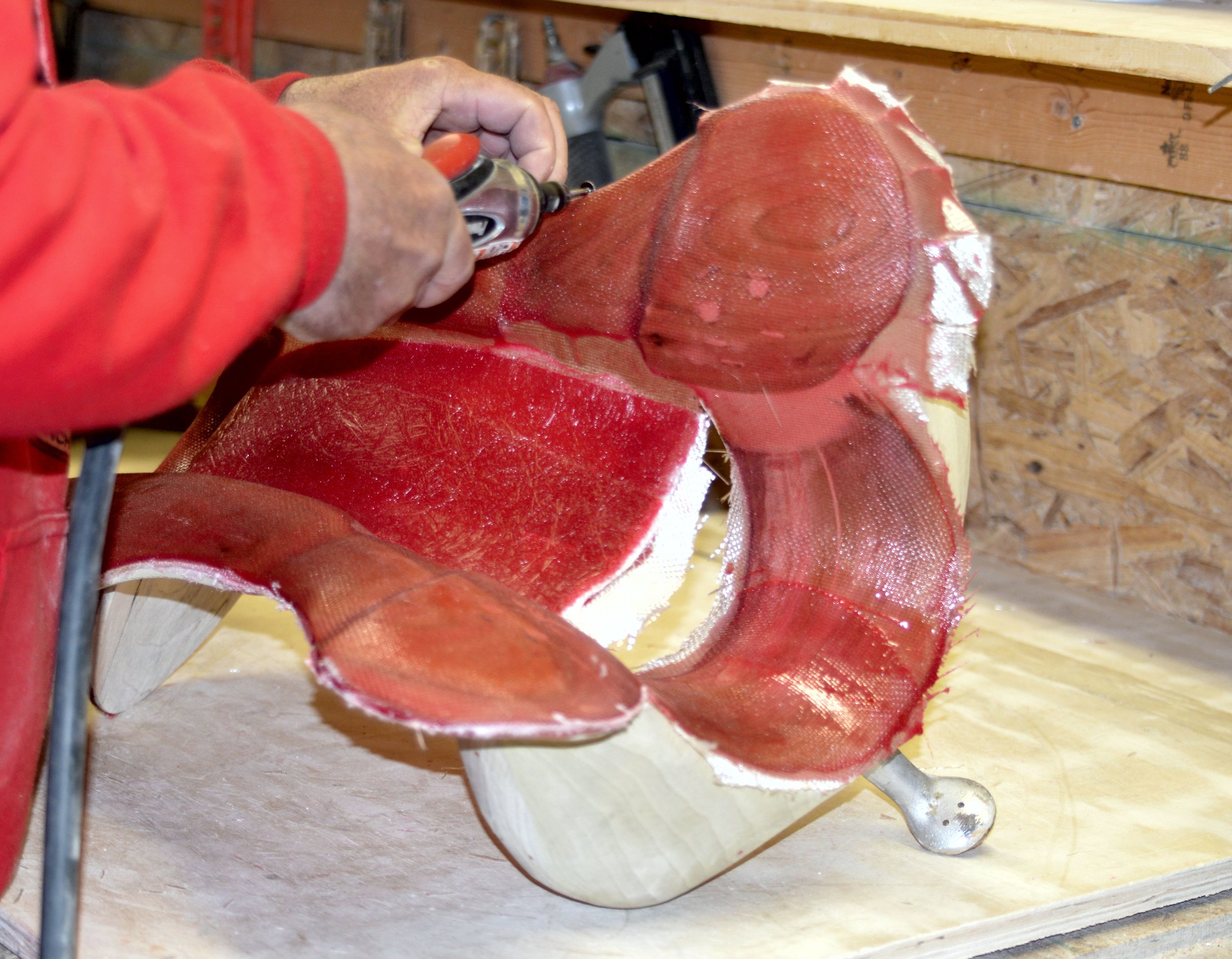
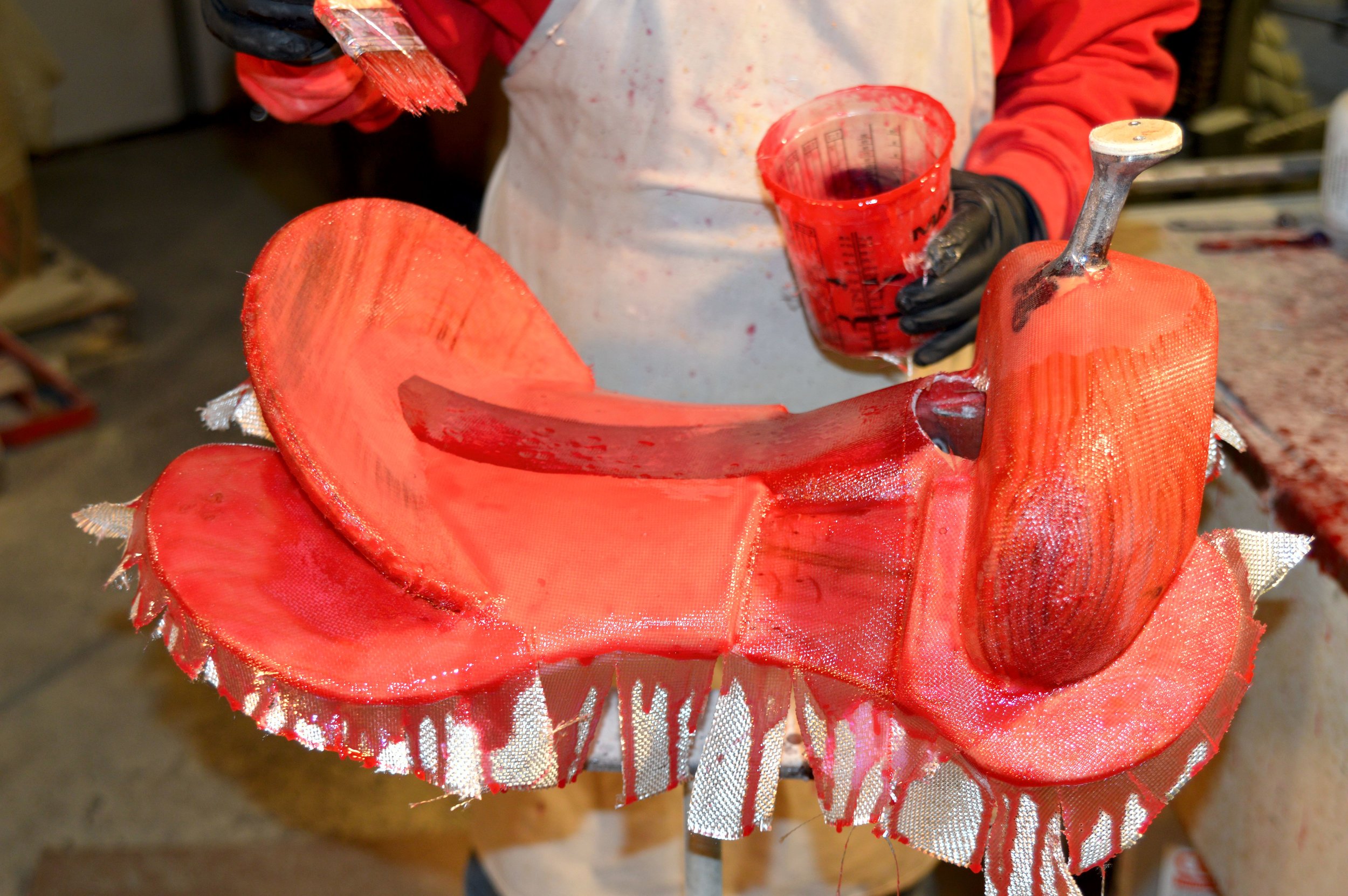
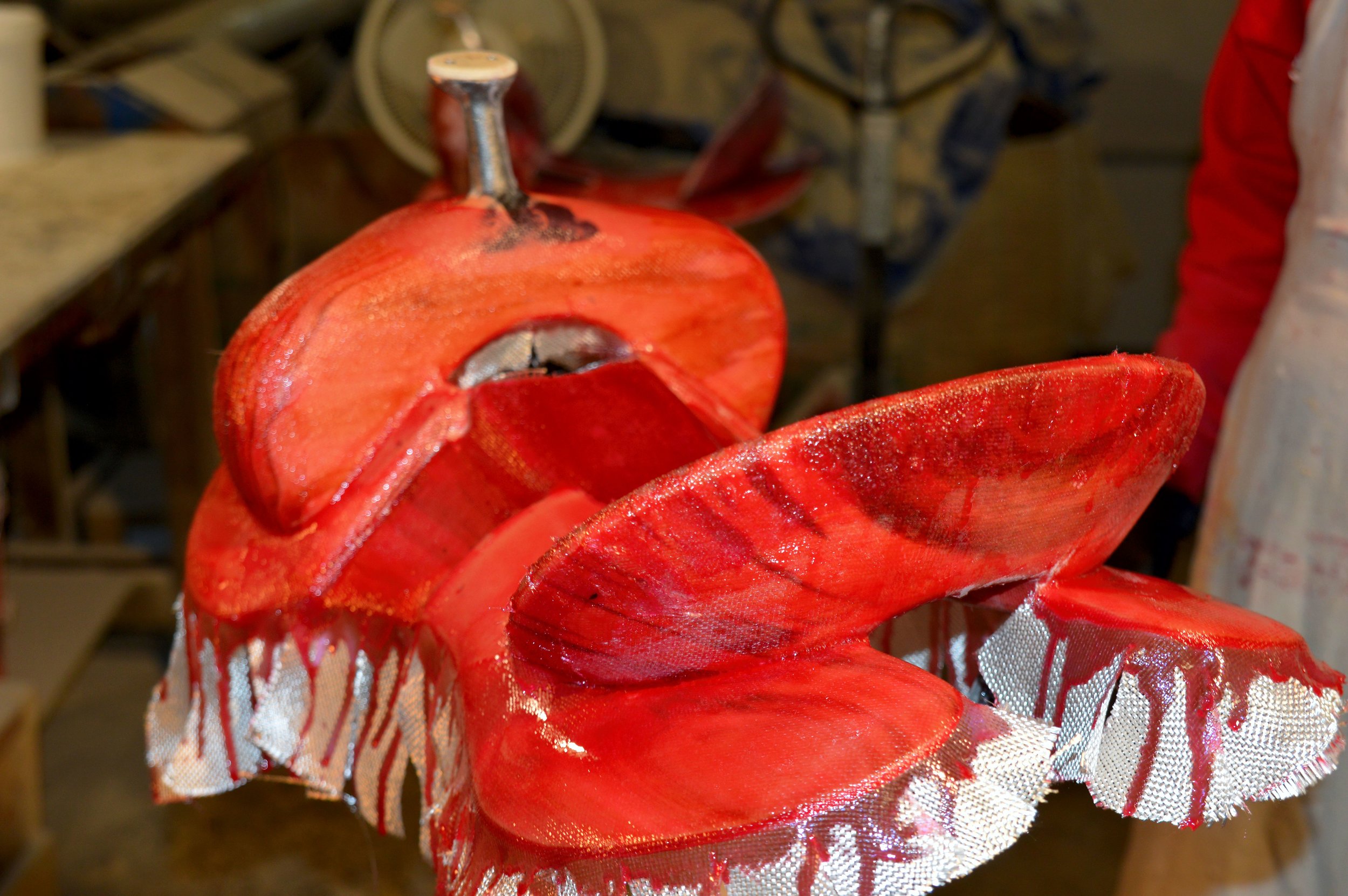
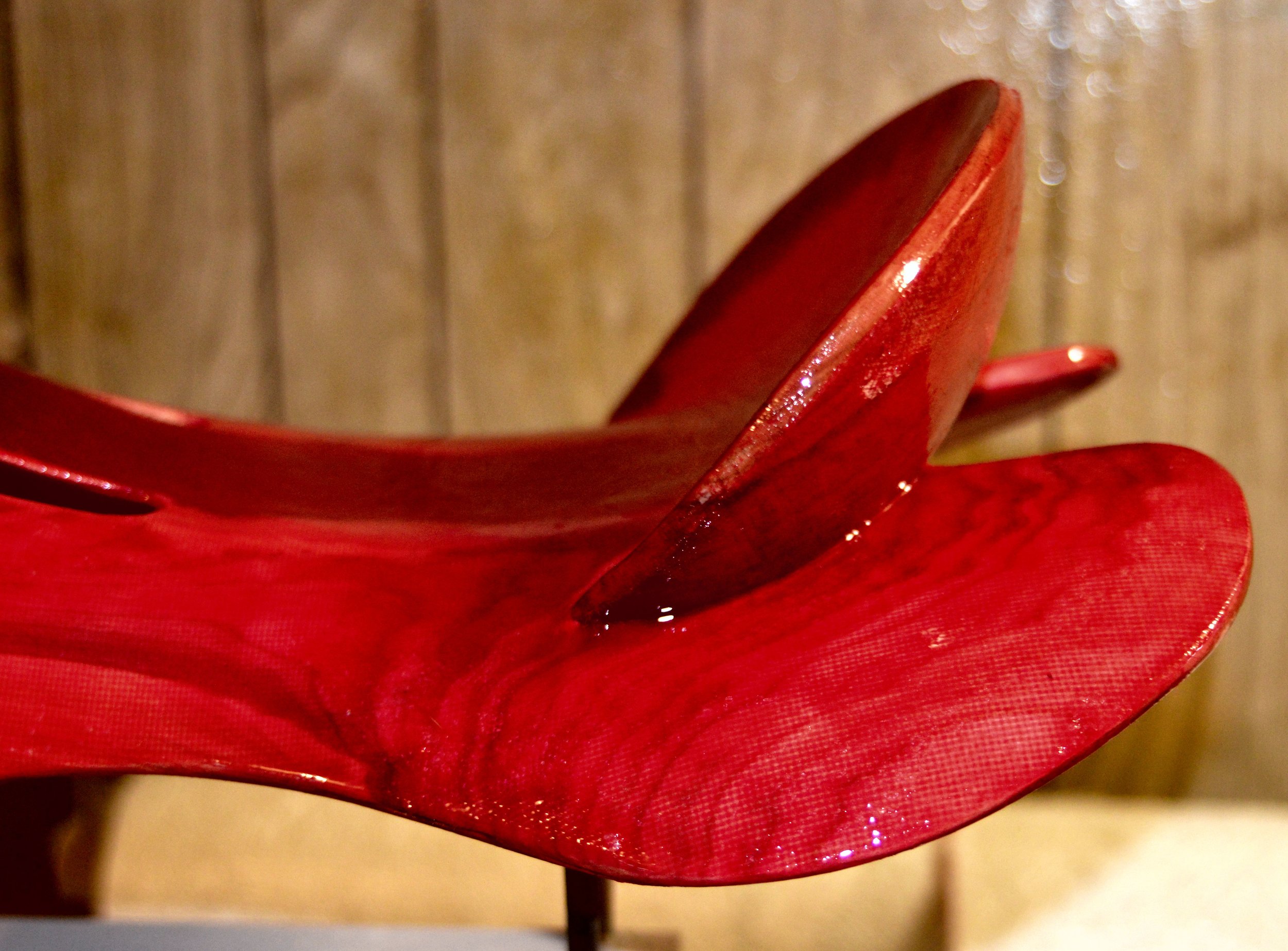
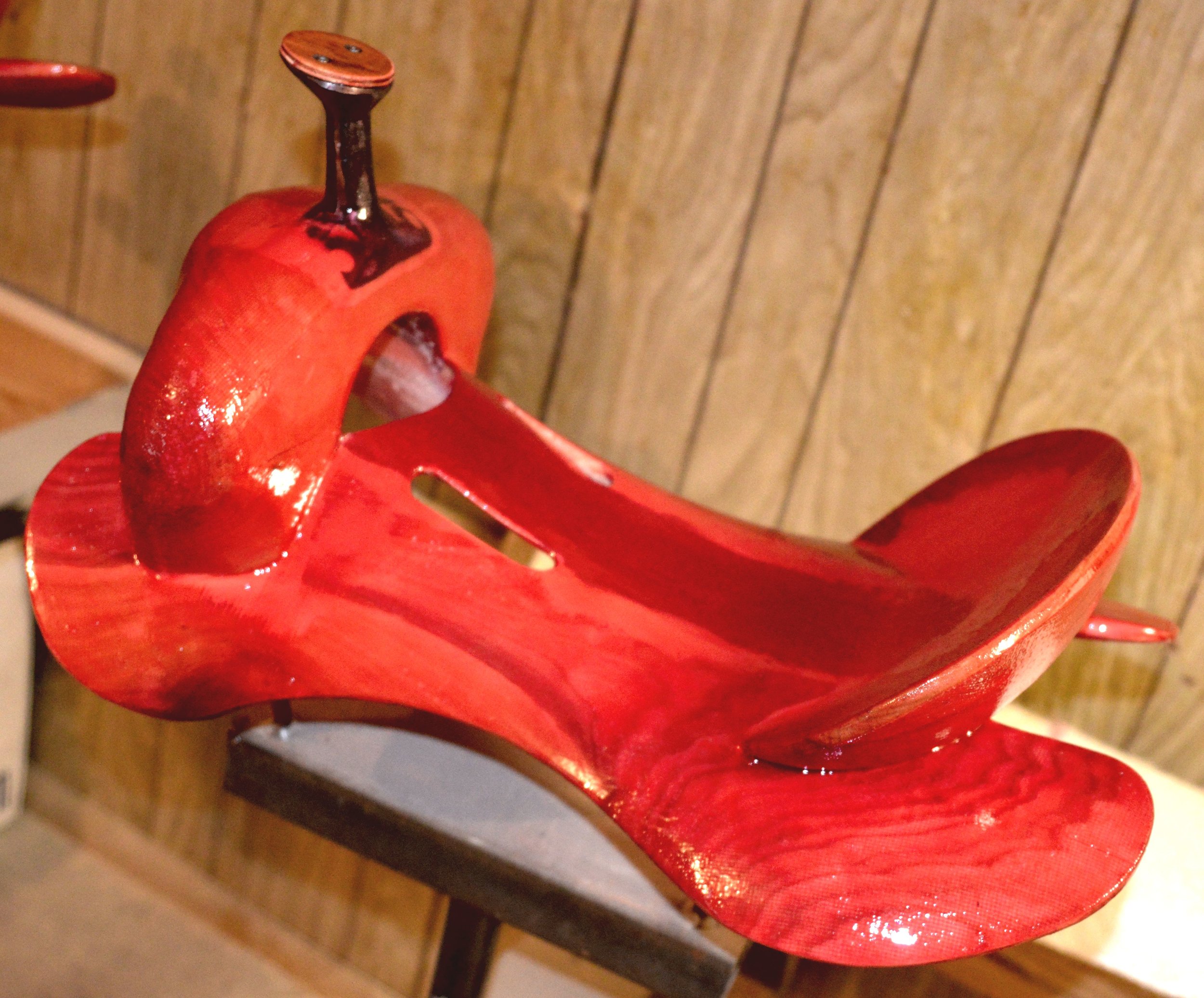
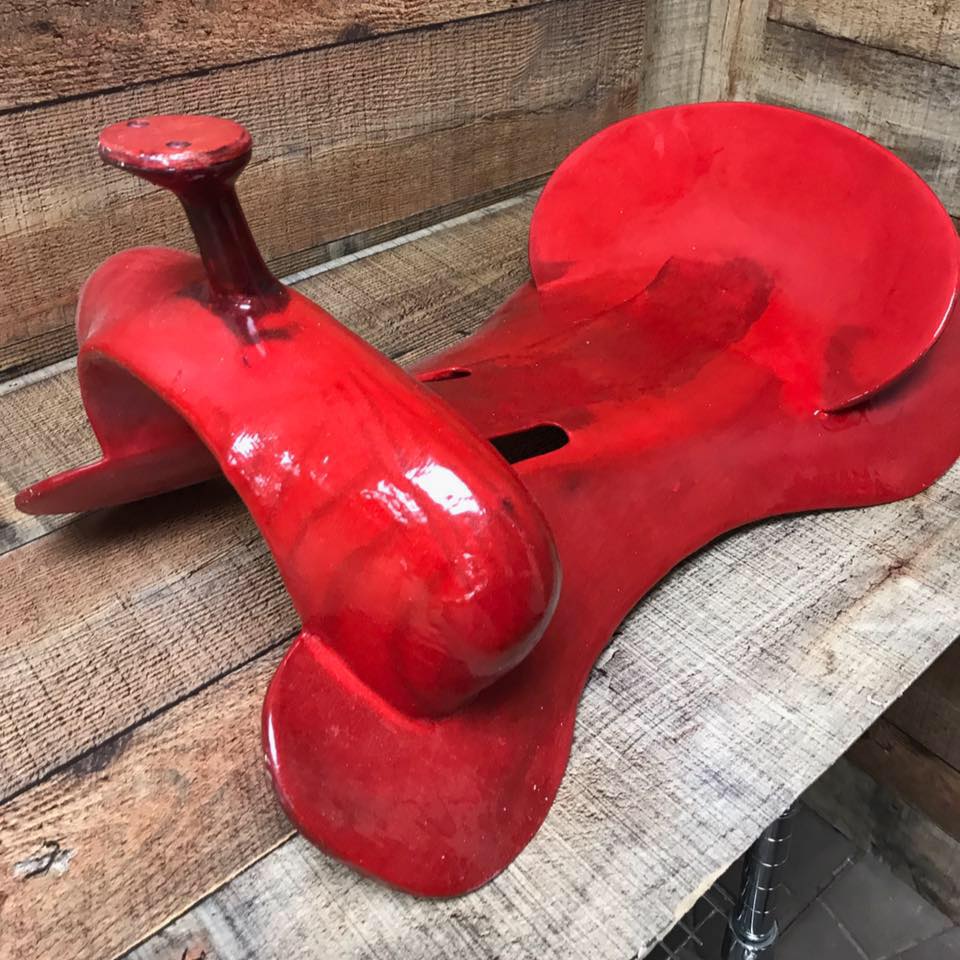